The Essentials of Welding Table Top
When I first ventured into the world of metalworking, the importance of a solid Welding Table Top quickly became apparent. It’s like the stage where your creative sparks fly, quite literally!
A good welding table isn’t just a flat surface; it’s a fortress for your projects. With a sturdy metalworking surface, you have the perfect platform to conquer those ambitious creations, ensuring that everything stays put as you work your magic.
I’ve learned that material matters. Steel is my go-to for a fabrication table because it can withstand the heat and the weight of whatever I throw at it. Remember that flimsy tables just won’t cut it; they’re a recipe for disaster!
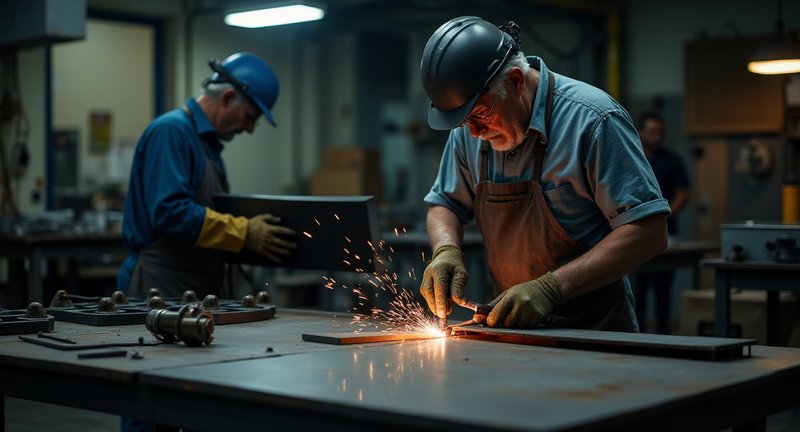
Speaking of disasters, I once attempted to weld on a makeshift table. Let’s just say, the results were less than stellar. A welding table that can absorb the chaos of your craft is essential; it’s like having a trusty sidekick by your side, ready for action.
Don’t forget the little details! A well-designed welding workbench often features slots and holes for clamping your workpieces securely. These features may seem minor, but they transform the experience from frustrating to fluid.
In the end, investing time and thought into your welding platform can make all the difference. Whether you’re a seasoned pro or a curious beginner, this vital piece of equipment is your gateway to achieving spectacular results in your metalworking adventures.
Choosing the Best Welding Table Top
Concerning crafting a perfect workspace for metalwork, the surface is everything. I’ve learned through trial and error that the right surface can elevate your projects from ordinary to extraordinary.
Imagine working on a flat, sturdy base that doesn’t warp or bend under pressure. A well-crafted surface allows you to lay out your materials with confidence, knowing they’ll stay in place while you focus on your creative vision.
Think about the materials you’re using. A high-quality, heat-resistant option is essential, especially if you’re planning on fusing metal. I once had a table that was far too flimsy; every spark made me hold my breath, praying it wouldn’t buckle.
Don’t overlook the size. It’s tempting to go small for convenience, but trust me, you’ll regret it when your projects start piling up. I’ve found that a generous area makes all the difference when assembling larger pieces.
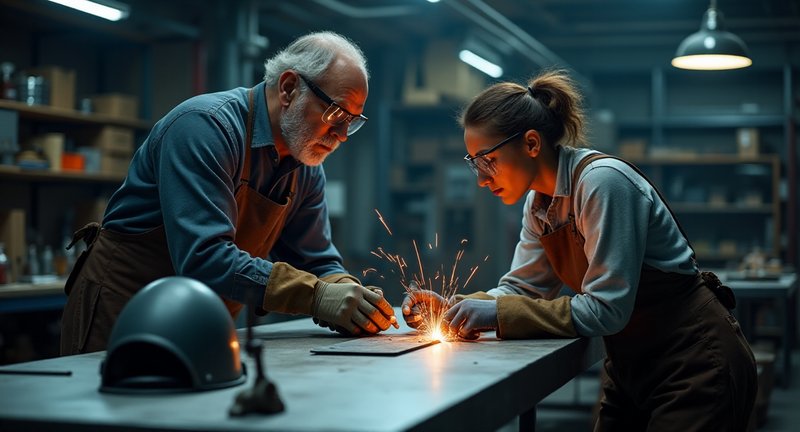
Another vital factor is the finish. A smooth surface allows for easy cleanup and prevents unnecessary scratches. I remember the first time I spilled some welding slag; it took ages to clean up and left me cursing my choice of material.
Also, consider portability if you plan to move your workspace around. A lightweight yet sturdy option can be a game changer for setting up in different locations.
Choosing the right surface can transform your crafting experience, and I can’t stress enough how much it influences your final product.
Introduction to Creating a Sturdy Work Surface
When diving into the world of creating a sturdy work surface, there’s something almost meditative about the process. As I embarked on this journey, I found that the right foundation can transform your workspace from a mere table to a realm of inspiration and productivity. Here’s how to lay the groundwork for a resilient surface that can handle any project.
1. Selecting Your Material
- Metal Sheets: Durable and resilient, ideal for heavy-duty tasks.
- Plywood: Versatile and easy to work with, great for various projects.
- MDF: Smooth surface, perfect for crafting or painting.
- Particle Board: Cost-effective and lightweight, good for lighter tasks.
- Glass: A sleek option that’s easy to clean and adds a modern touch.
2. Dimensions and Design
- Height: Consider your comfort. A height of 36 inches is often ideal for most tasks.
- Width and Length: Ensure there’s enough space for your tools and materials. Aim for at least 4 feet by 2 feet for versatility.
3. Stability is Key
- Legs: Use sturdy materials such as steel or hardwood. They provide the essential support.
- Bracing: Cross-bracing can enhance stability, particularly for larger surfaces.
- Leveling Feet: Adjustable feet ensure that your work surface stays even, even on uneven floors.
4. Finishing Touches
- Surface Treatment: A coat of varnish or paint not only protects but also adds personality.
- Storage Solutions: Integrate shelves or drawers to keep your space organized.
By creating a robust work surface, you’re not just building a table; you’re crafting a sanctuary for your creativity. It’s a place where ideas flourish and projects come to life. So, roll up your sleeves and get ready to make something great!
Importance of a Quality Workbench for Welding
When I first dipped my toes into the fiery world of welding, I quickly discovered that having a sturdy workspace was crucial. A quality workbench isn’t just a luxury; it’s the very foundation of your craft, where sparks fly and creativity ignites.
Picture this: you’re standing at your workbench, tools scattered about like an artist’s palette, and you feel the comforting weight of solid construction beneath your elbows. The right surface supports your projects, allowing you to maneuver with ease and confidence. It’s all about creating a sanctuary for your craft.
Let’s not forget about safety. A well-designed workspace keeps you grounded, preventing slips and spills that could lead to costly mistakes or worse. I can’t stress enough how a stable platform can mean the difference between a project well done and a haphazard mess.
Also, a great workbench can be an inspiration in itself. The sight of your materials neatly organized and your tools at arm’s reach can spark new ideas and encourage innovation. It’s like having a blank canvas, waiting for you to create something extraordinary.
In my experience, investing in a solid workspace pays off in spades. It enhances efficiency, boosts creativity, and ensures safety all essential ingredients for a successful welding journey. So, if you’re serious about your craft, consider what a quality workbench can do for you. Trust me; it’s a game changer.
Choosing the Right Materials for Your Work Surface
In the context of creating the ideal work surface for your projects, choosing the right materials is paramount. From personal experience, I’ve learned that not all surfaces are created equal. The material you select can greatly influence your workflow, precision, and overall enjoyment. So, let’s dive into some exciting options!
-
Steel Plate: This is a heavyweight champion. It can handle intense heat, heavy impacts, and won’t warp under pressure. If you’re into serious projects, this is your go-to. Just remember to keep it clean and rust-free.
-
Aluminum Sheet: Lightweight yet durable, aluminum can be a game-changer for those who value portability. It’s easy to work with and offers a slick surface that can be machined, making it perfect for intricate designs. Plus, it won’t rust!
-
Composite Materials: Think of the magic that happens when various materials come together. Composites can offer a unique blend of strength, heat resistance, and lightness. They’re excellent if you’re looking to tailor your work surface to specific projects.
-
Wood Laminates: Don’t underestimate the charm of wood! While it’s not heat resistant, laminated wood surfaces can provide a fantastic base for lighter projects. Plus, the aesthetic appeal of wood can’t be beaten.
-
Glass: This one might surprise you! A tempered glass surface can offer a sleek, modern touch to your workspace. It’s easy to clean and looks fantastic, but just be cautious of its fragility.
Choosing the right material is like picking the right ingredients for a recipe. Each surface has its unique flavor and characteristics. So, think about your projects and select a work surface that enhances your creativity and efficiency. Happy crafting!
Essential Tools Needed for Construction
With respect to construction, having the right tools is like having a well-tuned orchestra. Each instrument plays its part in creating a harmonious masterpiece, and trust me, I’ve learned that the hard way.
First off, let’s talk about the workbench. It’s your stage, where all the magic happens. A sturdy surface can be the difference between a project that’s a joy to work on and one that’s a headache waiting to happen.
Next up, clamps are your unsung heroes. They keep everything in place while you bring your vision to life. I can’t tell you how many times I’ve found myself in a dance with these little devices, wrestling with stubborn materials that refuse to cooperate.
Now, don’t overlook the importance of quality hand tools. A reliable set of chisels and saws can turn even the most mundane tasks into a delightful challenge. Trust me, investing in good tools is like having a secret weapon up your sleeve.
And let’s not forget safety gear! It’s not just about looking the part; it’s about keeping yourself in one piece. A good pair of goggles can save you from a splintered adventure gone wrong, and ear protection is a must-have if you enjoy your hearing.
Also, keep a sturdy storage solution handy. Having a place for everything not only declutters your workspace but also makes you feel like a pro. After all, a tidy space is a happy space, and it fuels creativity like nothing else.
So, as you embark on your construction journey, remember: the right tools can transform the ordinary into the extraordinary.
Step-by-Step Guide to Building Your Workbench
Building your own workbench is like setting the foundation for every project you’ll undertake. I’ve been down this road, and I can tell you, there’s something immensely satisfying about crafting the very place where all your future creations will come to life. So, where do we begin? Let’s break it down into digestible steps:
-
Design the Layout: Start by sketching out your ideal workbench. How much space do you need? Will you have shelving or drawers underneath? Think about your primary tools and how often you use them. My tip plan for versatility.
-
Gather Materials: Once your blueprint is ready, it’s time to choose materials. Plywood or hardwood for the surface, sturdy 2x4s for the legs, and don’t forget some heavy-duty screws and bolts. You want this thing to last!
-
Cut and Measure: Measure twice, cut once that rule applies here more than ever. When cutting wood for the frame, precision is key. Use clamps to hold everything steady, and don’t rush this part. I’ve learned the hard way how uneven cuts can throw off the entire project.
-
Assembly: Now for the fun part putting it all together. Assemble the legs first, securing them to the frame, and then attach the surface. Make sure it’s level. Trust me, an uneven workbench can make even the simplest tasks frustrating.
-
Finish Strong: As a matter of fact, consider adding a coat of varnish or sealant to protect your workbench surface. If you’re like me, this table will see a lot of action, so a little extra protection goes a long way.
Your new workbench should reflect the way you work organized, sturdy, and ready for anything.
Selecting the Best Thickness for Your Work Surface
Selecting the right thickness for your work surface is crucial, especially when you’re considering a Welding Table Top. From my experience, this decision can make or break your project’s efficiency. Trust me, you don’t want a table that warps under heat or dents easily from dropped tools. So, how do you choose the best thickness? Let’s dive into it.
Key Factors to Consider:
-
Type of Work: If you’re working on light-duty projects think thin metals or small crafts then you can probably get away with a thinner top, around 3/16 inch. However, for heavier jobs like fabrication or working with large metal pieces, you’ll need a sturdier surface, typically 1/4 inch or thicker.
-
Heat Resistance: Welders know that heat can cause metal to warp, especially thinner sheets. A thicker Metalwork table surface (let’s say 1/2 inch or more) will handle heat much better, ensuring your surface stays level and durable over time.
-
Budget vs. Durability: I get it, thicker metal means a higher cost. But consider this investing in a thick top now will save you from having to replace it down the line. Opt for 3/8 inch as a middle ground if you’re unsure. It strikes a balance between durability and affordability.
Materials That Matter:
- Steel: If you ask me, steel is your best bet. It’s resilient and readily available.
- Aluminum: Lightweight, but prone to damage under high heat.
- Cast Iron: Heavy-duty but difficult to move or adjust.
When choosing the right thickness, think about your workspace’s future. Are you expanding? Going pro? The right Steel workbench top can evolve with your needs. Don’t shortchange yourself by picking something too thin, trust me it’s not worth it.
How to Measure and Cut Your Materials Properly
In relation to measuring your materials, precision is your best friend. There’s nothing more frustrating than getting halfway through a project only to realize things don’t quite line up. From my experience, a solid tape measure is a must-have, but I’ve learned the hard way that measuring twice really does save time.
Cutting your materials can feel like an art form. You want to be smooth but deliberate. Whether you’re using a saw or a laser cutter, I always tell people to work with patience and focus. It’s tempting to rush, but trust me, uneven edges will haunt you later.
One trick that has served me well is marking your cut lines with a bold, clear marker. Don’t be shy with your markings. A faint pencil line might leave you guessing, especially when sparks are flying and things get hectic.
If you’re working with metal, don’t forget about clamping. You want everything locked down tight before you start slicing away. Not only does this prevent your material from moving around, but it also helps you achieve that clean, straight cut we all dream of.
In the end, it’s about taking control of your process. Trust your tools, trust your measurements, and don’t be afraid to slow down. A steady hand and a calm approach can turn a good project into a great one.
Techniques for Joining and Securing the Surface
In the matter of joining and securing surfaces, especially in any hobby where precision is key, mastering a few smart techniques makes all the difference. I’ve spent countless hours refining these skills, and I can tell you it’s not just about getting things to stick together. It’s about creating a bond that stands the test of time, both structurally and visually. Here are a few methods I’ve found particularly effective:
-
Clamping: The secret sauce for a seamless fit. The right clamps prevent any movement while securing surfaces, ensuring a tight, even bond. Quick tip: make sure to check for excess glue or material that might squeeze out during the process.
-
Riveting: If you’re looking for extra strength, especially with metals, riveting is a go-to method. It not only fastens materials but also creates a solid, unyielding joint. Rivets, once set, add an aesthetic industrial touch that’s hard to beat.
-
Brazing: Think of this as a more delicate approach compared to traditional welding. Using a filler metal with a lower melting point, you can bond materials without risking damage to the pieces themselves. It’s perfect for when you need a strong but subtle join.
-
Epoxy adhesives: When welding or brazing isn’t an option, and clamps alone won’t cut it, epoxy comes in handy. This stuff binds like no other and works across a range of materials from wood to metal to plastics. Apply, clamp, and let it set. You’ll be left with a joint that’s as tough as nails.
Experimenting with different techniques allows you to tailor your approach to the project’s unique needs. And believe me, once you get the hang of these, you’ll feel like a surface-joining wizard in no time.
Finishing Touches: Smoothing and Sealing
Let’s dive into the final phase: the finishing touches. When you’re aiming for a professional-grade surface, this stage is non-negotiable. It’s not just about aesthetics it’s also about ensuring durability and functionality.
Smoothing the Surface
First up, you’ll want to give the surface a good smoothing. I’ve found that starting with a high-grit sandpaper, like 320 or even 400, works wonders to eliminate any rough spots or micro-burrs. I usually go in a circular motion, but a back-and-forth method also does the trick, depending on the material. Don’t rush this step! Slow and steady pressure is key to avoid accidentally gouging the surface.
For those tight corners or awkward edges, a hand file is your best friend. It gives you that control that power tools sometimes lack. Just be gentle; finesse is more important than brute force here.
Sealing for Longevity
Now, once everything’s smooth as silk, it’s time to seal the deal literally. Choosing the right sealant is crucial, especially if your piece will be exposed to heat, moisture, or even the elements. I’m partial to a silicone-based sealant for its heat resistance, but if you want a clear finish, go for polyurethane.
- Waterproof sealants for outdoor use
- Heat-resistant sealants for high-temperature applications
- Epoxy coatings for an ultra-durable, scratch-resistant finish
Apply the sealant in thin, even layers. I typically use a foam brush to minimize streaks, but a spray-on option works great for large, flat surfaces. Let it cure fully patience is key here, as rushing can lead to imperfections that are tough to fix later.
There’s a real satisfaction in completing these finishing touches, knowing you’ve given your project the polish it deserves.
The Key Insights on Welding Table Top
When you’re in the zone, crafting that perfect weld, having the right workspace can make all the difference. I’ve spent countless hours adjusting, tinkering, and fine-tuning my setup, and through this, I’ve discovered what truly matters in a quality surface for welding. Let’s break it down, so you don’t have to learn the hard way.
First, think about material. Stainless steel and cast iron are go-to choices, but if you’re like me and prefer something that’s durable yet portable, you might lean toward a sturdy steel option. It resists warping from heat and offers just the right balance between weight and sturdiness.
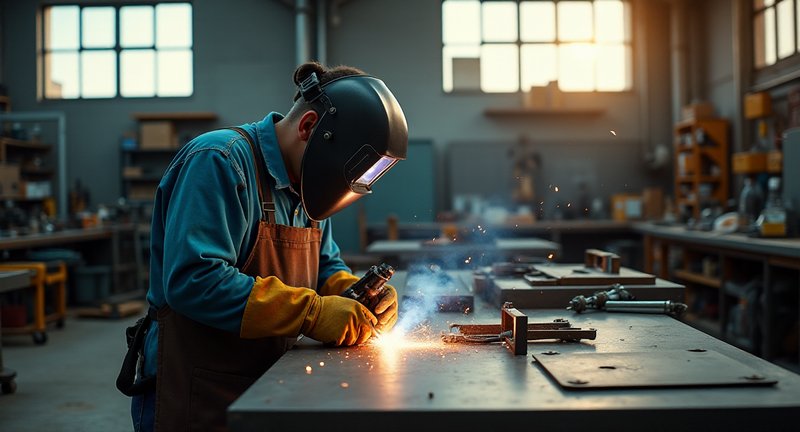
Key features to consider:
- Flatness: This might sound basic, but the flatter your surface, the more precise your welds. Trust me, there’s nothing worse than chasing uneven seams because of a warped platform.
- Adjustability: Some surfaces allow for height or tilt adjustments, which can save your back and your patience. If you’re working on varied projects, flexibility can be a game-changer.
- Clamping system: Being able to secure your work without hassle is essential. Look for options with built-in slots or holes designed for easy clamping.
- Mobility vs. Stability: If you need to move your workbench around, wheels can be a nice feature. However, don’t sacrifice stability for convenience nothing kills a project faster than a wobbly surface.
As a matter of fact, don’t forget about maintenance. A little attention to cleaning and rust prevention will keep your surface in tip-top shape, ensuring every weld is as clean as the first.
Take it from me investing time into picking the right work surface can elevate your entire welding experience. Choose wisely, and your projects will thank you.
Customizing Your Work Surface for Welding Projects
With regard to setting up a workspace for your welding projects, you really want to make the space your own. It’s not just about throwing together a random surface and calling it a day. Oh no! If you want to weld like a pro (or at least feel like one), then customization is key. You’ll thank yourself later when everything’s in place and works like a well-oiled machine.
Start by considering the materials. Steel surfaces work wonders since they can handle high heat, but what if you want something more specific? Here are a few things to think about:
- Non-flammable surfaces: Safety is first, my friend. Always. Avoid materials that could catch fire or melt when exposed to sparks.
- Clamping points: A few strategically placed cutouts or clamps go a long way when holding metal in place. Trust me, nothing’s worse than chasing a stubborn piece around while welding.
- Adjustable height: Do yourself a favor and either invest in or build a surface that’s height-adjustable. Whether you’re standing or sitting, your back will thank you after hours of working.
- Built-in storage: Why not have a few drawers or hooks underneath? That way, your tools are always within arm’s reach instead of scattered all over.
I’ve found that organizing your surface isn’t just about ease of use it also improves the quality of your welds. When everything’s secure and accessible, you’ll spend more time focusing on your work and less time searching for tools or adjusting pieces. Your work surface can truly be a game-changer for productivity. Plus, a little customization makes it feel like your space a workshop built just for your needs.
Adding Features: Clamps, Vises, and More
Clamps and vises are the unsung heroes of any workspace. They keep things steady when everything else seems chaotic, giving you that crucial extra hand. Trust me, without them, it’s like trying to juggle with one arm tied behind your back.
When I first added a quality vise to my setup, it felt like unlocking a new level. Suddenly, projects that needed precision became far less nerve-wracking. I’m telling you, nothing beats the feeling of knowing that your material isn’t going to slip out at a critical moment.
Speaking of upgrades, adding a range of clamps transformed how I worked. With them, I can hold down multiple parts without breaking a sweat. It’s not just about speed; it’s about accuracy, too. The more secure your workpiece, the sharper your end result.
But there’s more to this than just clamping and holding. Sometimes, it’s about thinking ahead. A pivoting vise, for instance, offers that flexibility when you’re working from tricky angles. It’s like a game-changer in the middle of a tough job one move, and suddenly, everything becomes more manageable.
For those who take things a step further, integrated features like magnetic holders or quick-release clamps can shave minutes, even hours, off a project. It’s all these little things that accumulate to make a workshop feel complete. In the end, these tools don’t just help; they become extensions of the craftsman’s hands.
Tips for Maintaining Your Work Surface
Keeping your work surface in good shape is one of the most underrated aspects of hobby maintenance, especially if you’re tackling projects that involve sparks, heat, or heavy materials. Trust me, I’ve learned this the hard way after neglecting mine for too long. Let me share a few key tips that will keep your workspace pristine and functional for years to come.
First, regular cleaning is essential. You’d be surprised at how quickly dust, debris, or metal shavings build up. Take a few moments after each session to wipe everything down with a non-abrasive cloth or brush. This habit not only extends the life of your work surface but also keeps your projects clean.
Here are a few extra pointers to think about:
-
Protective Layering: Use a mat, sheet, or heat-resistant cover when dealing with materials that could scratch or damage the surface. Even a simple fireproof blanket can make a world of difference.
-
Rust Prevention: If your work area is made of metal, a light coat of oil or wax can help prevent corrosion, especially if you’re working in a humid environment. Don’t go overboard just a thin layer will do the trick.
-
Avoiding Overload: Never use your work surface as a dumping ground. Piling tools, materials, or scrap parts on it increases the risk of accidental damage. Hang up your tools or store them properly when they’re not in use.
Also, inspect your surface regularly for any signs of wear and tear. Early detection of dents, chips, or rust spots can save you from bigger headaches down the road.
Knowledge Base
What can I use for a welding work surface?
For a welders’ table top, the most common materials used are steel and cast iron. Steel, particularly mild or carbon steel, is preferred due to its durability, heat resistance, and ease of cleaning. Cast iron is another option known for its flatness and vibration dampening qualities. However, some welders might use stainless steel for specific projects due to its corrosion resistance, although it’s typically more expensive. A solid, flat surface ensures proper welds and workpiece stability.
How thick should steel be for metal fabrication surface?
The steel used for a welding station surface should ideally be at least 3/8 inch (around 9.5 mm) thick. This thickness provides a sturdy and stable work surface that can withstand the high heat generated during welding. For heavier-duty applications, many welders prefer 1/2 inch (12.7 mm) steel to avoid warping and to ensure a longer lifespan of the table. A thicker surface offers better durability and stability when clamping or hammering materials.
What is the best table surface for welding?
The best table surface for welding is typically a flat steel top, as steel is highly resistant to heat and easy to ground for electrical work. Mild steel is the most popular choice due to its affordability and strength. Cast iron is also excellent for its flatness and shock absorption. Stainless steel, while more resistant to rust, can be cost-prohibitive and less common. In general, a flat, conductive, and heat-resistant surface makes for the best welding table.
Why are welding tables so expensive?
Welding tables are expensive because they require high-quality materials that can withstand heat, support heavy workpieces, and remain flat under extreme conditions. Materials like thick steel or cast iron, precise fabrication, and sometimes integrated features like clamping slots, leveling feet, and tool storage increase costs. Additionally, manufacturing processes that ensure long-term durability and precision contribute to the price. The investment in a welding table is justified by its longevity and ability to improve the accuracy and safety of welds.
Can you use aluminum top on welding table?
While aluminum is not typically used for welding platforms, it can be used under specific conditions. Aluminum has a lower melting point and is more prone to warping under high heat compared to steel, making it less ideal for general welding work. It also doesn’t conduct electricity as effectively for grounding purposes, which is crucial in welding setups. However, for lightweight or specific aluminum projects, some welders may opt to use an aluminum surface, though it’s not recommended for heavy-duty welding.
How do I keep my welding work surface from rusting?
To prevent rusting on a welders’ table top, regular maintenance is key. Applying a thin layer of machine oil or WD-40 can create a protective barrier against moisture. Some welders use a paste wax to seal the surface, offering both rust prevention and lubrication for smoother work. Regularly cleaning the table to remove any debris or metal particles will also help reduce rust buildup. Keeping the table in a dry environment further prevents corrosion.
Can you use stainless steel top for welding table?
Yes, a stainless steel top can be used for a welding table, though it is less common due to its higher cost. Stainless steel offers excellent resistance to rust and corrosion, which is beneficial in humid environments or for long-term durability. It’s also easy to clean. However, for general welding tasks, mild steel is preferred because it’s more cost-effective. Stainless steel tables are often reserved for specialized welding projects or in industries where cleanliness and rust prevention are essential.
Can welder sit on welding table?
It’s generally not recommended for a welder to sit on a welding table due to safety concerns. Welding tables are often part of an electrical circuit, and sitting on one can increase the risk of electric shock. Additionally, welding operations can involve heat, sparks, and sharp metal edges, which can pose injury risks. It’s important to ensure the table is used for its intended purpose, and proper safety measures, such as grounding and protective gear, are always followed.
How far apart are the holes on a metal fabrication surface?
The holes on a welding station surface are typically spaced in a grid pattern with distances ranging from 2 to 6 inches apart, depending on the design. Commonly, a 2-inch grid spacing is used for smaller or more precise projects, while larger tables may have a 4- to 6-inch grid for more flexibility in clamping. These holes allow for versatile clamping positions, making it easier to secure workpieces during welding. The uniform spacing ensures compatibility with various clamping tools and accessories.
What surface can you weld on?
You can weld on various surfaces, but a conductive, heat-resistant surface is essential. Steel, particularly mild or carbon steel, is the most popular choice for welding tables because it withstands high temperatures and provides a strong, flat platform for clamping and grounding. Cast iron is also used for its stability and vibration resistance. Non-flammable surfaces like concrete can be used as well, though they lack the conductivity needed for grounding, making them less ideal for welding setups.
I couldn’t agree more about customizing your workspace! When I first started welding, I didn’t put much thought into it and just used whatever was available. Big mistake! Once I invested in a sturdy, adjustable surface, and added some clamping points, it made such a difference in how smooth my projects went. I used to spend way too much time chasing parts around, like you said, but now it feels like everything is in sync. Also, the built-in storage tip is genius! I’m constantly misplacing tools, so having them right there would save me so much hassle. Thanks for the practical advice – definitely making some tweaks to my setup now!
Spot on! Having the right workspace for welding can really make or break your project. I’ve been in situations where an uneven surface totally wrecked my welds, so flatness is absolutely something I prioritize now. I also appreciate the focus on adjustability height and tilt adjustments save me so much hassle when I’m working on different pieces. I’ve added wheels to my bench for portability, but stability is a must. It’s all about striking that balance, and you captured that perfectly! Maintenance is a great call-out too. Rust can sneak up on you, and keeping everything clean has saved me a lot of headaches in the long run. Investing in a good surface really does pay off over time.
This section on finishing touches really speaks to me! There’s something incredibly satisfying about smoothing a surface until it’s perfect. I’ve always used sandpaper in circles, too, and silicone sealants are my go-to for any heat-resistant projects. And yes, patience with the sealant curing process is key I’ve learned that the hard way. Love the foam brush tip, definitely going to try that next time!
I totally agree about the importance of clamping! I used to rush through that part and ended up with messy joints. Now, taking a bit more time to clamp everything perfectly has completely changed my game. Also, epoxy adhesives are a lifesaver. Such great advice here!
Wow, I really felt that part about uneven cuts haunting you later it’s so true! I’ve learned to take my time and mark clearly with a bold line too, especially after making some messy mistakes in the past. Clamping is another game-changer, especially when working with metal. Locking things down tight makes all the difference for precision. Great tips here!
You’re absolutely right about the importance of picking the right thickness for a welding table top. I’ve made the mistake of going too thin before, and the warping was a nightmare! I now swear by 1/4 inch steel for most of my projects it’s a great balance between durability and cost. I also appreciated your breakdown of materials. Steel is definitely my go-to, but I’ve been curious about cast iron for those heavy-duty jobs. Although I guess the weight would be a hassle to move around! Thanks for the insights, this really made me rethink some of my future setups.
I couldn’t agree more with how satisfying it is to build your own workbench! It’s like creating the backbone for all your future projects. I recently built mine, and the tip about planning for versatility is spot on. Shelving and drawers underneath were lifesavers for organizing my tools. Every DIY enthusiast should start with this essential piece!
Haha, I totally feel you on the clamps! It’s amazing how such a small tool can have such a massive impact on your projects. I’ve had more than a few “fights” with materials that just won’t stay in place without a good set of clamps. I’ve learned the hard way that having the right tools really does make a difference between frustration and smooth sailing. Your comparison to a well-tuned orchestra is spot on!
I love how you’ve broken down the different material options for work surfaces! It’s like a mini-guide for anyone who’s serious about crafting. Steel plate is definitely my go-to for heavy-duty projects. I had no idea aluminum could be such a great choice for portability definitely something I’ll consider for lighter, more intricate designs. And I’ve got to say, the glass idea totally caught me off guard! It’s such a unique option. I’m not sure I’d trust it for heavy work, but it sounds like it could add a super sleek look to a more modern workspace. Great breakdown!
Oh man, I couldn’t agree more about the importance of a solid workbench! When I first started welding, I was using this wobbly old table, and it made every project a nightmare. The difference when I upgraded to a heavy-duty workbench was night and day. It’s so true what you said about it being a ‘sanctuary for your craft.’ There’s something about having a stable, well-organized space that makes the whole process feel more professional and, honestly, more fun.
Wow, this really resonates with me! The process of building a work surface is truly like creating a space for inspiration. I love how you broke it down into sections because every element whether it’s the height, material, or bracing plays such a huge role in making your workspace efficient and comfortable. I never used to think much about the legs or bracing, but after a wobbly table situation, I’m all about cross-bracing now! Also, adding storage solutions like shelves or drawers is genius! It helps keep everything organized and gives you more room to breathe while working. I’m definitely going to incorporate some of these ideas next time I upgrade my workspace. Thanks for the tips!
You’re so right about the size of the workspace! I used to work on a table that was way too small, and it felt like I was constantly juggling materials just to keep things from falling off the edges. Going for a larger surface area was the best decision I made it made my workflow so much smoother. Plus, I couldn’t agree more on the importance of having a heat-resistant surface. There’s nothing worse than feeling like your whole table is about to cave in when the sparks fly! Thanks for the reminder about portability too, I might look into getting something lighter for my mobile setup.
Oh man, I can totally relate to your experience with makeshift tables! The first time I tried welding, I used an old wooden bench that I thought would ‘get the job done’ spoiler alert: it didn’t. It ended up scorching the wood and I had to abandon the project halfway. Since then, I’ve become a big fan of steel for my welding table too. You’re right, a solid surface like that makes all the difference in stability and durability. It’s like having a reliable friend who holds your hand steady while you work. I also love how you highlighted the importance of the little design features, like the slots for clamping workpieces. That’s one of those things you don’t appreciate until you’re in the middle of a project, trying to keep everything from sliding around! Honestly, a well-thought-out table is a game-changer for anyone who’s serious about metalwork. It’s one of those investments that keeps paying off every time you start a new project. Great advice all around!