The Basics of Crucible Furnace
When I first encountered the Crucible Furnace, I felt a spark of curiosity ignite within me. The allure of transforming raw materials into molten masterpieces was simply irresistible.
This fascinating device operates like a mini volcano, where intense heat turns metal into a glowing river. It’s mesmerizing to watch the transition from solid to liquid, as if you’re witnessing a magical alchemical process.
Setting up a Melting crucible is an art in itself. You need to ensure it’s on a stable surface, surrounded by safety gear, ready for your creative journey.
Once you’ve loaded it with your chosen metal, the anticipation builds. You can almost hear the furnace hum with excitement as it prepares to unleash its fiery potential.
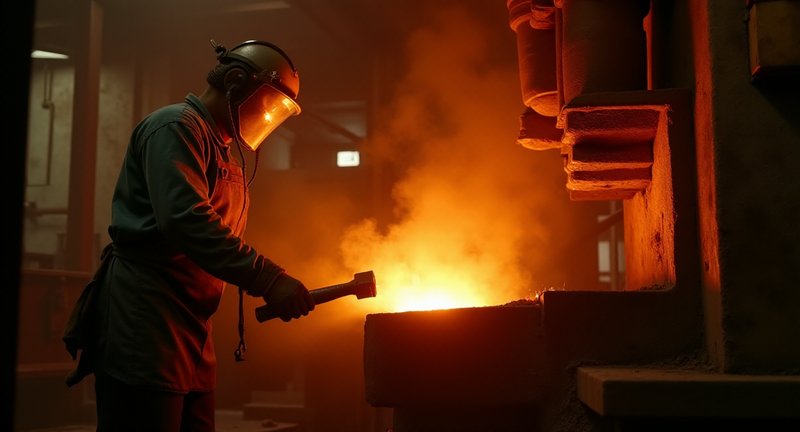
As the temperature climbs, I often find myself lost in thought. It’s a moment of reflection, contemplating the transformation that awaits, both in the metal and in my own crafting journey.
As a matter of fact, when the time is right, pouring the molten metal feels like a ceremonial rite. It’s not just about the end product; it’s about the thrill of the entire process.
Whether you’re a seasoned pro or a novice, the Metal forge holds endless possibilities. Embrace the journey, and let your imagination run wild.
The Role of a Crucible Furnace in Metalworking
When diving into the world of metalworking, the fiery heart of the process is truly captivating. Imagine a vessel, glowing and bubbling, transforming raw materials into brilliant metals. This indispensable tool serves several key functions that I’ve come to appreciate over time:
-
Melting Metal: The primary role is to liquefy metal, allowing it to be molded into desired shapes. Watching this transformation is mesmerizing; it’s like witnessing a caterpillar become a butterfly.
-
Alloying: Mixing different metals creates unique properties. The ability to blend materials opens up a universe of possibilities for new creations. Picture combining copper and tin to forge bronze it’s a game-changer.
-
Refining: The heat helps remove impurities, resulting in a purer final product. This step is crucial for achieving that perfect shine and durability in your metalwork.
In my own experience, understanding how to harness the power of this tool has elevated my projects. I remember my first attempt at casting nerves and excitement dancing in my chest. With a little patience and practice, I learned to respect the temperature and timing. Each pour feels like a personal victory, a little piece of art that comes alive.
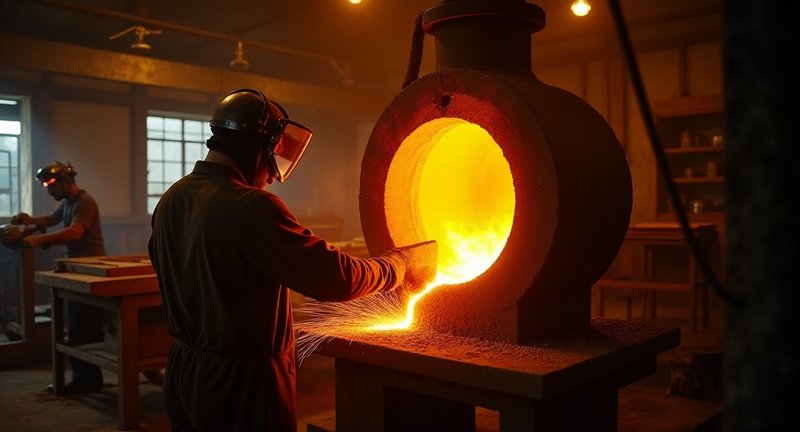
If you’re considering venturing into this realm, I highly recommend diving deep into the nuances of this fiery vessel. It’s more than just a machine; it’s a gateway to creativity and craftsmanship. Trust me, the journey is worth every moment spent in the glow of molten metal.
Introduction to Metalworking and Heating Methods
Metalworking is an enchanting dance of fire and creativity, where raw materials transform into exquisite pieces of art or functional tools. In my journey through this captivating realm, I’ve discovered various heating methods that ignite the imagination. Let’s realize some of these fascinating techniques, shall we?
Common Heating Methods in Metalworking
-
Forge: The heart of any blacksmith’s workshop. Here, the heat is generated by burning coal or gas, allowing you to shape metal with hammers and anvils.
-
Induction Heating: This method uses electromagnetic fields to heat the metal quickly and efficiently. It’s like giving the metal a warm hug that prepares it for transformation!
-
Oxy-Acetylene Torch: A powerful tool that produces a flame hot enough to cut and weld metals. It’s precision at its finest, perfect for intricate projects.
-
Resistance Heating: This technique employs electrical resistance to generate heat. Think of it as giving metal a cozy blanket of warmth, allowing it to be shaped and molded.
-
Heat Treating: Involves heating and cooling processes to enhance metal properties. It’s akin to giving the metal a spa day relaxing it and allowing it to emerge stronger!
As you explore these heating methods, remember that each brings a unique flavor to your projects. Whether you’re forging a sword or crafting delicate jewelry, the right technique can make all the difference. So grab your gear and get ready to embark on a thrilling metalworking adventure!
What is a Melting Pot?
When I first encountered the term ‘melting pot,’ I envisioned a bubbling cauldron where various elements converge, creating something entirely new. It’s a vibrant metaphor that speaks not just to cooking but to the fusion of cultures, ideas, and experiences.
In the essense of hobbies, a melting pot becomes a space where different interests blend harmoniously. Imagine a crafting session where knitters, painters, and scrapbookers share their passions, each contributing unique techniques and inspirations. It’s like a creative gumbo, where each ingredient enhances the flavor of the whole.
I recall attending a community art fair where this phenomenon unfolded before my eyes. Enthusiasts from various backgrounds showcased their talents, and I found myself entranced by the interplay of styles and mediums. The joy of collaboration sparked new ideas in my own creative journey.
Moreover, engaging in a melting pot experience can transform the way we perceive our hobbies. I’ve learned that sharing knowledge not only enriches my skills but also fosters a sense of belonging. It’s an exhilarating reminder that we’re all part of something larger, interconnected through our shared passions.
So, the next time you dive into your favorite pastime, consider inviting others into the mix. You might be surprised at the wonderful concoction that emerges. The beauty of a melting pot lies in its ability to celebrate diversity while uniting us in our quest for creativity and expression.
Benefits of Using a Melting Furnace
Using a melting furnace has changed the way I approach metalwork. It’s not just about the heat; it’s about unlocking a world of possibilities. When you experience the roar of a furnace, the process becomes almost meditative. You can feel the raw power of metal shifting form, and it’s something to behold.
One of the great joys of using a melting furnace is the control you gain. Temperatures reach levels unimaginable with regular tools, letting you melt down stubborn metals with ease. You get a real sense of mastery over the material, bending it to your creative will.
Efficiency is another huge advantage. With the right furnace, what used to take hours can be done in a fraction of the time. It’s like upgrading from a horse-drawn carriage to a rocket ship except this rocket lets you cast jewelry or forge art. And let’s be honest, we all like saving time.
But here’s the kicker the precision. The furnace gives you the perfect environment for consistent results. Whether you’re working with gold, silver, or something more industrial, the furnace will treat each metal with the respect it deserves.
Also, there’s a certain satisfaction in watching the transformation. It’s a feeling you can’t quite describe until you’ve experienced it yourself. That moment when the solid turns to liquid it’s like witnessing a bit of magic unfold before your eyes.
Essential Safety Equipment for Metalworking
When you dive into the world of metalworking, the sheer power of transforming raw materials into something useful or beautiful is truly electrifying. But before the sparks fly, safety needs to come first. Trust me, you don’t want to learn this lesson the hard way.
Let’s break it down to the essentials, shall we? Here’s what you’ll need:
-
Eye Protection: This isn’t negotiable. Metal shards and flying debris don’t give warnings, and your eyes are far too valuable to risk. Invest in quality goggles or a full-face shield think of it as armor for your vision.
-
Heat-Resistant Gloves: Don’t even think about touching hot metal without these. Get yourself a pair that can handle the heat without feeling like you’re wrapped in clunky oven mitts. Flexibility matters here.
-
Respirator Mask: The fumes and particles from grinding or welding? Yeah, they’re not something you want in your lungs. A proper respirator can make the difference between breathing easy and a potential health nightmare down the road.
-
Fire-Resistant Apron: Spattered metal burns, and the last thing you need is a hole in your clothes or worse, your skin. A solid, fire-resistant apron keeps you safe and adds a little swagger to your workshop look.
-
Ear Protection: If you enjoy your hearing and want to keep it intact, grab some ear protection. The sounds of grinding, hammering, and cutting aren’t kind to your eardrums.
Every one of these pieces is like a trusty companion, ensuring that you can push the limits of your creativity without the fear of injury. I always say: no project is worth losing a limb over, right?
Choosing the Right Melting Vessel
As it relates to melting metal, the vessel you choose is like the compass guiding your entire project. It’s not something you want to overlook or rush into. I remember my first attempt let’s just say it didn’t end well for the workshop floor.
The material of the melting vessel should be your top concern. You don’t want something that will warp or crack under high heat. It has to be resilient, but also a good conductor of heat. Ever tried using something too thin? You’ll be waiting forever, trust me.
Then, there’s the shape. Not just any old pot will do. You need something deep enough to contain the molten chaos but wide enough for easy pouring. It’s like picking the right bowl for cake batter, only the stakes are molten metal hot.
Don’t forget about the vessel’s lid. Sounds basic, right? But a lid can make or break your experience. It helps keep the heat in and protects the melt from contamination. Skipping the lid is like baking a cake without preheating the oven it just doesn’t work.
And, of course, the size matters. You’ve got to think about how much metal you’re working with. Too big, and you waste heat. Too small, and you’ll overflow. I’ve learned the hard way that trying to force too much metal into a small vessel is a recipe for disaster.
A Comprehensive Guide to Crucible Furnace
The Crucible Furnace is a curious beast in the world of metalworking. When I first encountered one, I was struck by its sheer simplicity and raw power. It’s one of those things you don’t fully appreciate until you’ve stood next to its glowing core.
This type of furnace doesn’t just melt metal it commands it. The process feels almost primal, as if you’re holding a conversation with fire itself. Working with a Metalworker’s forge is a dance between precision and chaos, and believe me, the furnace leads.
One thing I’ve learned over the years is that the right crucible can make or break your project. There’s a certain satisfaction in choosing the right material graphite, clay, or even silicon carbide. Each has its quirks, but they all bow to the same fiery master within the furnace.
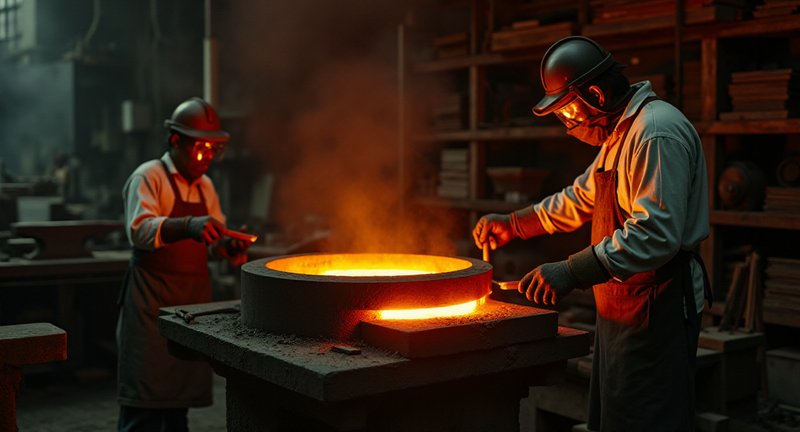
Of course, it’s not just about the melting. The Smelting crucible creates this unique atmosphere in the workshop both literal and metaphorical. It’s the warm heartbeat of any serious metalworking space. You can feel its presence even when it’s cooling down, like the coals of a campfire long after the flames are gone.
If you ever get the chance, don’t just stand back and watch. Get close (but not too close) and let the heat wrap around you. It’s one of those rare experiences where you truly feel the power of transformation in your hands.
Preparing Your Workspace for Metal Melting
Let’s be honest, preparing your workspace for metal melting is half the fun of the entire process. The excitement kicks in when you start imagining the fiery heat turning solid metal into a shimmering pool of liquid. But don’t get ahead of yourself yet. First, you’ll need to create a safe and organized zone.
I always start by clearing a dedicated area, preferably somewhere that won’t mind a little dirt and fire like a garage or backyard. The floor, though, needs to be concrete or similarly non-flammable. Believe me, a stray spark can lead to more excitement than you bargained for!
Ventilation is another must-have. Metal melting produces fumes, and you don’t want to be breathing that stuff in. A well-ventilated area is key, so get those windows wide open or set up a fan to push air out. Trust me, your lungs will thank you later.
And don’t forget about protective gear. Heat-resistant gloves, a face shield, and an apron aren’t just optional extras they’re your first line of defense. When you’re dealing with molten metal, you’ll want all the protection you can get. There’s nothing quite like the heat of molten metal it’s beautiful, but unforgiving.
Also, before I light the torch or ignite the flames, I double-check my tools. Tongs, stirring rods, molds they all need to be within arm’s reach. It’s all about smooth workflow when the metal’s hot. You’ll feel like a conductor in your own symphony of heat and metal when everything’s in place.
Setting Up the Heating Device
As for setting up your heating device, it’s all about precision and a bit of patience. Trust me, I’ve been through the trials of fumbling with wrenches, only to realize I forgot to check a crucial detail beforehand. But hey, that’s how we learn, right?
First things first, let’s talk location. You don’t want this thing near anything flammable, and ventilation is key – nobody wants to fill their workspace with mysterious fumes. My personal rule of thumb? At least a solid meter away from anything that might melt or catch fire.
Now, when you’re hooking it all up, follow these steps carefully:
- Stabilize your base: Make sure the device is on a flat, heat-resistant surface. A wobbly base is a recipe for disaster.
- Secure the fuel source: Whether you’re working with propane or something a bit more high-tech, make sure all connections are tight. Double-check – and I mean double-check – for leaks.
- Install the heat shield: If your device didn’t come with one, it’s worth investing in. You don’t want to feel like you’re roasting alongside your materials.
Once it’s all set up, take a step back. Does everything look right? Are all your safety checks in place? If you’re not sure, this is where it pays to pause and reassess. I’ve learned the hard way that rushing never leads to good things when heat is involved.
When you finally flip that switch, listen. If something sounds off or if you get an odd smell, shut it down immediately. The heat should come up smoothly – no wild pops or spurts. That’s how you know you’re on the right track.
Understanding Temperature Control
Temperature control is more than just watching a dial; it’s the difference between a successful project and one that melts down literally. When I first started, I underestimated how much mastery over temperature could impact the quality of a finished piece. Trust me, you don’t want to learn that lesson the hard way.
There are a few things you’ll need to keep in mind:
-
Heat Ranges: Not every material reacts the same to heat. Some metals demand a low, steady warmth, while others crave that fiery, glowing intensity. Getting the right balance is like knowing when to let your morning coffee cool a little just enough to avoid burning your tongue but still enjoy the heat.
-
Ventilation: Without proper airflow, your work environment will feel like a sauna, and your metals won’t heat evenly. It’s not just about comfort either; poorly ventilated spaces can lead to some dangerous gas buildups. Keep the air moving; your lungs will thank you.
-
Heat Retention: This is where things get a little tricky. You’ve got to keep the heat stable, even after turning down the intensity. It’s like trying to keep a campfire going add too much wood too quickly, and it smothers. Too little, and the flames flicker out.
When you get the hang of controlling temperature, you’ll find that the metal listens to you melting just when it should and hardening when you ask. And trust me, once you see that perfect glow, you’ll know you’re in control.
Types of Metals Suitable for Melting
With respect to melting metals, not every piece of scrap lying around is up for the task. Trust me, I’ve experimented more than once, and let’s just say… not all metals behave nicely in the heat! So, let me walk you through the types of metals that are best suited for melting, based on my personal trials (and a few minor disasters along the way).
Aluminum
Ah, aluminum – the starter metal for many home foundry enthusiasts. It’s lightweight, has a relatively low melting point (about 660degC), and flows like a charm when heated. You’ll find it in soda cans, old window frames, and sometimes even in cast cookware.
Copper
Copper is a step up in complexity. This reddish metal melts at around 1,085degC. It takes a bit more firepower to get it into a liquid state, but the payoff? Stunningly vibrant pours that produce eye-catching pieces. Plus, it’s easy to find in old electrical wiring and pipes.
Brass
A combination of copper and zinc, brass is another fun one to melt. It’s a little more temperamental due to the zinc content, which vaporizes easily at high temperatures. Keep a close eye on it as it melts – trust me, it’ll save you some frustration!
Lead
Lead is for those looking for something super easy. With a melting point of just 327degC, it practically melts just by looking at it. However, be cautious with this one, as lead fumes are no joke. Always work in a well-ventilated area if you’re playing with this metal.
So, there you have it – a few metals that have been melted and molded in my own workshop. Each one behaves differently, offering its own quirks and challenges. Which one will you melt first?
Melting Processes Explained
When I first ventured into the melting world, I was amazed by the fascinating processes that transform solid materials into shimmering liquids. Let me share a few insights I’ve gathered along the way.
Understanding Melting Processes:
-
Heat Sources: Melting requires a heat source that can reach high temperatures. Common options include:
- Electric induction heaters
- Propane torches
- Gas-fired burners
- Arc welders
-
Materials: Not all materials melt the same way. For example:
- Metals like aluminum have relatively low melting points (around 660degC).
- More robust materials, such as titanium, can require temperatures exceeding 1660degC.
-
Container Choices: The vessel you use to contain the material while it melts is crucial. Options vary, including:
- Graphite molds for high-temperature applications
- Clay-graphite pots for lower-temperature melts
- Silicon carbide containers for added durability
-
Safety Precautions: Melting can be a hotbed of hazards, so always keep safety at the forefront:
- Wear protective gear, including gloves, goggles, and an apron.
- Ensure proper ventilation to avoid inhaling harmful fumes.
- Have fire extinguishing tools on hand just in case.
I remember my first attempt; the excitement was palpable! Watching the material transform, it felt almost magical. The bubbling and swirling liquids were mesmerizing. Each melting session taught me something new, making me appreciate the intricate dance of heat and material.
If you’re diving into melting, embrace the process. Every pour and every bubble holds the potential for creativity!
Pouring Molten Metal: Techniques and Tips
Pouring molten metal is like capturing liquid fire; it demands respect and finesse. From my own explorations in this thrilling hobby, I’ve learned that mastering the art involves not just technique, but also an understanding of the materials. Here are some tips to ignite your molten metal journey:
-
Safety First: Protecting yourself is paramount. Always wear:
- Heat-resistant gloves
- A face shield or safety goggles
- Long sleeves and closed-toe shoes
-
Choose Your Metal: Different metals behave uniquely when heated. Consider:
- Aluminum: Great for beginners, it’s forgiving and melts at a lower temperature.
- Bronze: A bit trickier, but the results can be stunning.
- Copper: Offers beautiful finishes but demands precision in pouring.
-
Prepare Your Workspace: A well-organized space is key. Ensure you have:
- A sturdy table or workstation
- A fire-resistant surface
- Adequate ventilation to avoid inhaling fumes
-
Heat it Up: Heating the metal evenly is crucial. I often:
- Use a torch for smaller batches, ensuring a consistent heat.
- Preheat the mold to reduce thermal shock, resulting in a cleaner pour.
-
Pour with Precision: When you’re ready to pour, maintain a steady hand. Pour slowly and steadily, allowing the metal to flow gracefully into the mold. Remember, practice makes perfect!
Embarking on this molten adventure can be exhilarating, and each pour brings its own surprises. Embrace the process and enjoy the alchemy of transforming raw materials into art!
Cooling and Solidifying Cast Metal
Cooling and solidifying cast metal is a fascinating dance of science and artistry that I’ve come to cherish in my journey as a hobbyist metalworker. When molten metal reaches its desired temperature, the next step is crucial how we cool it can dramatically influence the final properties of the material. Here are some insights based on my experience:
-
Cooling Techniques:
- Air Cooling: The most straightforward method. Simply let the metal sit in the open air. This is perfect for simple projects but can be slow.
- Water Quenching: A rapid cooling method that involves submerging the metal in water. It’s exciting to see the steam rise as the metal transforms.
- Sand Beds: Burying your metal in sand can provide a controlled cooling environment, leading to a more even solidification.
-
Factors to Consider:
- Alloy Composition: Different metals solidify at varying rates. Knowing your material can prevent unwanted cracks or warps.
- Thickness of the Cast: Thicker sections cool slower, which may lead to uneven results. Thin sections can cool too quickly, risking brittleness.
- Ambient Temperature: A hot day versus a chilly evening can make a significant difference in how your metal solidifies.
As I stand by my workbench, I can’t help but feel a sense of anticipation with each pour. Watching the molten metal fill the mold is like witnessing a magic trick unfold. After cooling, the moment of truth arrives will the cast turn out as envisioned? Each piece tells a story of its own, shaped by the cooling process and my choices.
Solving Your Queries
What is a crucible in a furnace?
A crucible in a furnace is a container designed to hold materials that need to be melted or subjected to high temperatures. Typically made from materials with high melting points, such as ceramic or metal, crucibles are essential for processes involving metalworking, glassmaking, and other industries requiring high heat. They ensure that the contents remain contained and protected during heating, allowing for precise control of temperature and chemical reactions.
What are the advantages of a melting furnace?
High-Temperature furnaces offer several advantages, including efficient heating and precise temperature control. They allow for the melting of small quantities of materials, which is ideal for experiments or small-scale production. The design often promotes uniform heating, minimizing hot spots that can lead to inconsistent results. Additionally, metal casting furnaces are versatile, accommodating various materials and can be used for different applications, from metal casting to ceramics.
What are the disadvantages of ceramic furnace?
Despite their benefits, laboratory furnaces have some disadvantages. They typically have a lower capacity compared to larger furnaces, limiting the volume of material that can be processed at one time. Crucibles can also be prone to wear and damage, especially when subjected to extreme temperatures and thermal shock. Moreover, they may require more frequent maintenance and replacement, adding to operational costs in the long run.
What is the crucible used for?
Crucibles are used for a variety of applications, primarily in metallurgy, chemistry, and materials science. They are essential for melting metals and alloys, enabling precise alloy compositions and casting. In laboratories, crucibles facilitate high-temperature experiments involving chemical reactions. Additionally, they are used in glassmaking, ceramics, and for heat treatment processes, showcasing their versatility in industrial and scientific settings.
What is the purpose of heating the crucible?
Heating the crucible serves several important purposes. First, it prepares the crucible for melting the material inside by eliminating moisture, which can affect the quality of the final product. Additionally, pre-heating ensures that the crucible can withstand the high temperatures required for melting metals or other materials. This process also promotes even temperature distribution, reducing the risk of thermal shock and prolonging the crucible’s lifespan.
Where should you put a crucible when you are heating it?
When heating a crucible, it should be placed in a furnace or on a stable surface designed for high temperatures, such as a kiln shelf or a dedicated crucible stand. It’s essential to ensure that the crucible is positioned securely to prevent tipping or accidental contact with flammable materials. If using an open flame, maintaining a safe distance from combustible surfaces is critical to avoid hazards.
When would you use a crucible?
A crucible is used when high-temperature processes are necessary, such as melting metals for casting, conducting chemical reactions, or heat treating materials. They are commonly employed in laboratories for experiments that require precise temperature control. Additionally, crucibles are essential in the manufacturing of ceramics and glass, where the integrity and purity of materials are paramount. Their versatility makes them suitable for a wide range of industrial and scientific applications.
What is the temperature range of a melting furnace?
The temperature range of a high-temperature furnace can vary significantly depending on the materials being processed and the design of the furnace itself. Typically, metal casting furnaces can reach temperatures from around 1,200degF (650degC) to over 2,500degF (1,370degC). Specialized crucibles made from high-temperature resistant materials may withstand even higher temperatures, allowing for the melting of various metals and alloys, including refractory materials.
What is the efficiency of a ceramic furnace?
The efficiency of a laboratory furnace largely depends on its design, insulation, and heating method. Generally, melting furnaces are known for their efficient energy use, particularly when melting small amounts of materials. Their ability to maintain high temperatures with minimal heat loss contributes to overall efficiency. However, factors such as the type of crucible used, the heating rate, and the material being melted can influence performance and energy consumption.
What does firing a crucible do?
Firing a crucible involves subjecting it to high temperatures to ensure its strength and integrity before use. This process helps to eliminate any moisture or impurities that might affect its performance during melting. Firing also enhances the crucible’s thermal stability, allowing it to withstand the extreme conditions encountered during metal melting or chemical reactions. This preparation is crucial for achieving reliable and consistent results in various applications.
Why is a crucible used during heating?
A crucible is used during heating because it is designed to withstand extreme temperatures while containing molten materials safely. Its construction allows for uniform heat distribution, reducing the risk of thermal shock and ensuring that the contents are heated evenly. Crucibles are essential in processes such as metal melting and chemical experiments, as they maintain the integrity of the materials being processed and facilitate accurate temperature control.
How long does it take to heat up a crucible?
The time it takes to heat up a crucible varies based on several factors, including the crucible’s material, thickness, and the heating method employed. Typically, it may take anywhere from several minutes to over an hour to reach the desired temperature, depending on the furnace’s heating capabilities. Ensuring that the crucible is preheated properly is crucial for achieving optimal results in melting or processing materials.
Your comment was recorded and is awaiting moderation.