An Introductory Look at Shino Pottery Glaze
As a pottery enthusiast, diving into the world of Shino Pottery Glaze has been nothing short of a mesmerizing journey. Originating in Japan during the 16th century, this glaze is renowned for its rich textures and earthy hues, creating pieces that are as unique as they are beautiful.
What sets Shino apart from other glazes? Here are some captivating characteristics:
- Variability: Each application results in a distinct finish. No two pieces are identical, which adds to their charm.
- Complex Colors: Ranging from bright oranges and reds to creamy whites, the palette is vast and versatile, allowing for creative expression.
- Surface Texture: The glaze often showcases a remarkable surface quality, ranging from smooth and glossy to rough and rustic, inviting touch and admiration.
In my own experiences, I’ve found that working with Japanese shino glaze requires a keen understanding of its nuances. Achieving that perfect balance can sometimes feel like alchemy playing with temperature, kiln atmospheres, and even the clay body can yield astonishing results.

Tips for getting started:
- Experiment with Different Clays: The base clay affects how the glaze interacts, leading to unexpected surprises.
- Vary the Application Techniques: Try dipping, brushing, or spraying. Each method produces a different effect.
- Kiln Atmosphere Matters: Shino often flourishes in reduction firing, where the kiln’s environment can influence the final outcome.
As you embark on your own Shino adventure, remember: patience and experimentation are your best allies. The allure of this glaze lies in its unpredictability, promising delightful revelations in every piece you create.
The Art of Shino Pottery Glaze
As I embarked on my journey into the world of ceramics, I found myself irresistibly drawn to a particular style of glaze that dances with the light and captures the essence of nature. There’s something magical about the rich, earthy hues and the unpredictable surfaces that evoke a sense of wonder and tranquility.
In my hands, the clay transforms, becoming a canvas for experimentation. Each firing reveals surprises, as if the kiln were a sorcerer casting spells of color and texture. The way the glaze flows and settles is akin to watching a watercolor painting come to life, the pigments merging and mingling in delightful chaos.
I’ve learned to embrace the beauty of imperfection; the drips and runs tell stories of the process. Every piece feels alive, as though it has a personality shaped by its journey through heat and time. It’s a reminder that art is not about precision but rather about expression and feeling.
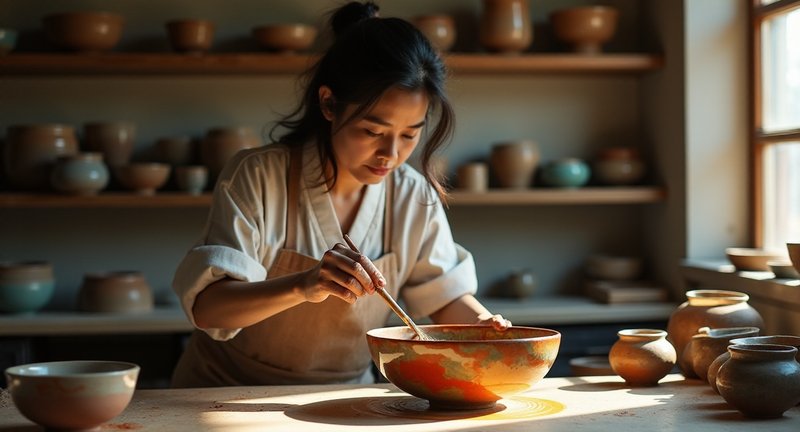
One afternoon, while sitting at my potter’s wheel, I recalled my first encounter with this vibrant style. I was captivated by the way it reflected the surrounding landscapes, echoing the warm tones of autumn leaves or the soft blush of a sunset. It was a moment of connection a dance between the earth and the artist.
If you’re considering exploring this glazing technique, I encourage you to play with your materials and let intuition guide you. Each experiment can lead to a new discovery, adding depth to your artistic repertoire and a touch of magic to your creations.
Introduction to Shino Glazing Techniques
As I dipped my brush into the luscious cream of traditional glaze, I felt the same thrill as a painter before a blank canvas. There’s something magical about the rich, warm tones that emerge, hinting at the stories each piece will tell.
With each stroke, I’m reminded of the alchemical dance that occurs in the kiln. It’s like watching a sunset transform the sky; each piece reveals its true nature only after enduring the intense heat.
When experimenting with different firing techniques, I discovered the sheer unpredictability of this art form. You never quite know if you’ll unveil a masterpiece or a beautifully flawed experiment.
Sometimes, I play with layering glazes to create depth. The interplay of textures and colors is reminiscent of a painter’s palette, begging for attention and appreciation.
The way these glazes interact with the clay body creates an aesthetic symphony. It’s as if the earth itself whispers secrets through the surface of my creations.
In this craft, patience is not just a virtue; it’s a necessity. As I await the final reveal, I can’t help but feel the anticipation build like the swell of a favorite song before the chorus hits.
Every piece is a gamble, an adventure into the unknown. I encourage you to dive into this captivating world and discover your unique voice through these vibrant, organic colors.
The History and Tradition of Shino Glaze
Ah, the art of Shino! My journey into this enchanting glaze began with a deep curiosity for the alchemical dance between clay and fire. Originating in Japan’s Mino region during the 16th century, it’s a mesmerizing blend of earthy hues that tell tales of tradition.
As I explored the process, I was captivated by how this glaze, with its creamy surface and fiery red-orange undertones, transforms during firing. Each piece emerges like a phoenix from the kiln, showcasing unique patterns that are as unpredictable as nature itself. It’s like uncovering a hidden treasure with every glaze application!
What truly fascinates me is the spiritual connection artisans have with their work. The careful selection of materials, the rituals of preparation, and the contemplative silence while waiting for the kiln to work its magic all contribute to the tradition’s rich context. Each creation feels alive, imbued with the artist’s essence and the whispers of centuries past.
I often ponder how the distinct characteristics of this glaze its ability to create a soft sheen or a rugged texture reflects the duality of existence. The interplay of simplicity and complexity is a reminder of life’s intricate nature.
So, if you ever find yourself exploring the world of ceramics, take a moment to appreciate the magic behind this remarkable glaze. It’s more than just a finish; it’s a dialogue between the maker, the material, and the fiery embrace of the kiln.
Characteristics of Shino-Style Finishes
When I first stumbled upon the unique world of Japanese ceramics, the characteristics of a certain style truly captivated me. There’s a magical quality to those earthy finishes, a vibrant dance between warmth and texture that instantly draws you in.
The surface often displays an organic randomness, as if nature itself decided to lend a hand. Each piece appears to tell a story, showcasing a variety of hues, from soft peaches to deep rusts, complemented by those charming speckles that glisten like stars in a night sky.
What strikes me the most is the layering effect glossy drips mingling with matte finishes. It’s as if the pottery is wearing a rich, colorful cloak, inviting you to run your fingers over its surface and feel the sensations it evokes.
Sometimes, I find myself mesmerized by the unpredictable results that arise from the firing process. Each creation is a testament to the artist’s skill, yet it humbly reveals its own personality. This delightful imperfection transforms the ordinary into extraordinary.
If you’re curious about this aesthetic, I urge you to explore it firsthand. Visit local galleries or try your hand at crafting your own pieces; you might just find yourself enchanted by the experience.
Embrace the journey of discovery, and you might uncover a deeper connection to the artistry behind these remarkable finishes.
Understanding the Ingredients of Shino Glaze
When I first ventured into the world of ceramic glazing, the allure of a certain glaze captured my imagination. It’s an enchanting mix of ingredients that dance together, creating a unique surface that tells a story with every piece.
The primary component is a mineral called feldspar. This gritty little marvel acts as the backbone of the glaze, helping it melt and flow during firing. Think of it as the canvas upon which the glaze’s character emerges.
Next, we have kaolin, the white clay that lends its magic to the mix. This ingredient not only contributes to the texture but also influences the glaze’s overall opacity. I often marvel at how a touch of this clay can transform the glaze, giving it a creamy depth that seems to breathe life into my creations.
Another key player is silica, the sparkly ingredient that brings a twinkle to the eye of the glaze. Silica plays the role of a glass former, ensuring that everything fuses beautifully during the intense heat of the kiln. It’s like the secret spice in a beloved recipe that elevates the final dish to new heights.
Also, let’s not forget the metallic oxides, those colorful wizards that add vibrant hues. Iron oxide, for instance, brings warmth and richness, while other oxides can introduce unexpected shades that surprise and delight. It’s a thrilling adventure, each batch revealing different results, akin to unwrapping a gift.
In my journey of experimentation, I’ve discovered that mastering this glaze isn’t just about the ingredients it’s about embracing the unpredictable nature of the firing process. Each piece becomes a unique testament to the alchemy of art and nature.
The Application Process for Shino Glaze
Ah, the enchanting journey of applying that beloved earthy glaze! It’s a tactile experience that combines intuition and artistry. When I first discovered this craft, the application process felt like a dance between chaos and control.
Before you begin, it’s essential to prepare your piece properly. Ensure that your clay body is bone-dry and free from dust. Trust me; that little detail can make a world of difference in how the glaze adheres.
Once you have your canvas ready, it’s time to explore the application techniques. I’ve always found dipping to be the most exhilarating method. It allows for rich depth and a luscious texture that brushing sometimes can’t capture.
If you opt for brushing, take your time. Each stroke should be deliberate, coaxing the glaze into every nook and cranny. I remember the first time I brushed on that glimmering finish. It felt like I was painting a dream, and every layer brought me closer to the vision in my mind.
Now, the real magic happens as the piece enters the kiln. Watching the transformation is akin to witnessing a caterpillar become a butterfly. The heat unlocks colors and textures, breathing life into your creation.
Don’t rush the drying process either! Allow your masterpiece to cool down slowly. I learned this the hard way, as I once tried to handle a piece too soon and learned the lesson of fragility.
Every time I embark on this glazing adventure, it’s a reminder of the beauty in imperfection. Each piece tells its story, revealing the personality of the glaze and the artist behind it.
Dive Deeper into Shino Pottery Glaze
Diving into the world of Shino Pottery Glaze is like stepping into a vibrant landscape of colors and textures that tell a story. Each glaze is a character, with its own personality, waiting to reveal itself on your ceramic canvas.
When I first experimented with this glaze, I was captivated by the way it dances with light. The warm hues ranging from fiery oranges to subtle creams are reminiscent of the sun setting over a serene Japanese landscape.
The beauty of Shino ceramic finish lies not only in its aesthetic charm but also in its unpredictability. There’s a thrill in the firing process, where the kiln becomes a magical box that transforms humble clay into something exquisite. You never quite know how the glaze will behave, and that’s part of the adventure.
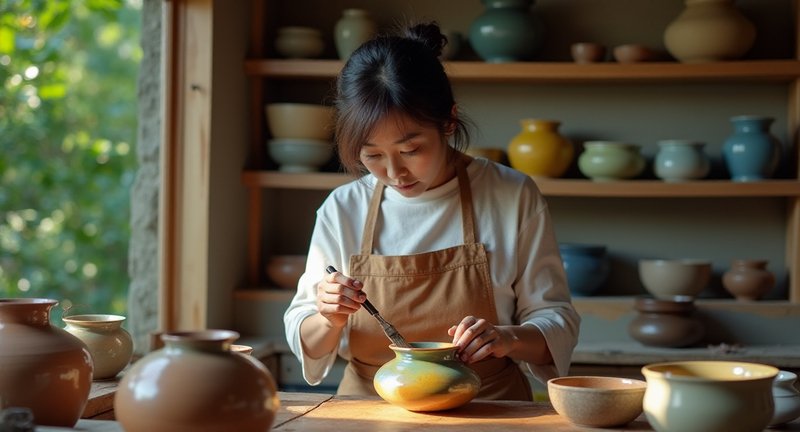
As I played with different application techniques, I discovered the delight of layering glazes. Each layer can interact, creating a depth that seems to pulse with life. It’s almost like painting with liquid sunshine, where the final result often takes my breath away.
I invite you to explore this journey of self-expression through Shino glaze technique. The process can be messy and unpredictable, but therein lies the joy of creation. Let the glazes inspire you, and embrace the happy accidents that happen along the way.
In every piece, there’s a piece of my heart and soul, and I hope your journey into Shino pottery brings you as much joy as it has brought me. So, pick up that brush, and let your creativity flow!
Tips for Achieving the Perfect Shino Effect
Achieving that sought-after Shino effect in your pottery can feel like a delightful treasure hunt. I remember the first time I successfully pulled it off oh, what a revelation! Here are some tips that I’ve gathered along the way to help you on this creative journey:
-
Understand the Base Clay: The choice of clay is foundational. Go for a stoneware that is rich and coarse. The texture will greatly influence how the glaze reacts during firing.
-
Experiment with Thickness: Application thickness can alter the final result dramatically. Try layering the glaze in different areas. A thicker application will give you that vibrant, luscious surface, while a thinner coat will offer a more subtle, delicate look.
-
Control Your Firing Temperature: This is where the magic happens. Aim for a reduction atmosphere in your kiln. A range of 2300degF to 2400degF (1260degC to 1315degC) is often where you’ll find that perfect sweet spot for dramatic surface effects.
-
Play with Timing: The timing of your reduction can also shape your glaze. Reducing early in the firing can yield a bright orange hue, while reducing later might offer deeper, richer shades. Don’t be afraid to experiment!
-
Seek Inspiration: Sometimes, the best ideas come from the most unexpected places. Flip through art books, wander through galleries, or even explore nature. Inspiration can strike when you least expect it!
Every potter has their unique approach, so remember that practice makes perfect. Embrace the journey, savor the process, and don’t hesitate to let your creativity flow. You’ll find your personal style emerging as you refine your technique.
Happy glazing!
Exploring Color Variations in Shino Finishes
Exploring color variations in those earthy, rustic finishes can feel like embarking on a treasure hunt. Each piece, a canvas, tells a story through its hues and textures, whispering secrets of the firing process.
I remember the first time I laid eyes on those vibrant oranges and deep reds, shimmering like embers in a fire. It was a revelation, seeing how different firing atmospheres could transform a humble clay body into a celebration of color.
As I began experimenting, I noticed that layering techniques could create a dance of shades, each brushstroke unveiling a new surprise. There’s something magical about how a touch of iron oxide can morph into a vibrant crimson, while subtle shifts in temperature breathe life into that rich, brown undertone.
One particularly memorable piece was the result of an unexpected moment. I had left a bowl in the kiln a bit longer than intended, and when it emerged, it wore a mesmerizing gradient that flowed from a soft peach to a deeper russet. It was as if the kiln had decided to play artist, making me feel like a lucky spectator of this alchemical transformation.
Diving into the world of color variations, you’ll often find that the magic lies not just in the application but in the kiln’s embrace. Each piece holds a history, a fusion of creativity and chance, inviting you to explore its unique charm.
So, whether you’re drawn to those fiery oranges or the subtle whispers of earth tones, each finish offers a glimpse into the infinite possibilities of expression. Let your imagination guide you as you discover the kaleidoscope of colors waiting to be unveiled.
Shino Glaze in Contemporary Ceramics
Exploring the captivating world of glazes has always been a thrilling journey for me, especially when it comes to the rich and complex nature of a certain rustic finish that originated in Japan. In contemporary ceramics, this glaze has resurfaced with a modern twist, captivating both artists and collectors alike. Here’s why I find it absolutely enchanting:
-
Versatility: This glaze offers an unparalleled range of colors and textures, from creamy whites to vibrant oranges and deep reds. Depending on the firing technique and clay body, the results can be astonishingly varied, making each piece uniquely expressive.
-
Surface Character: The interplay of iron oxides and other minerals in the glaze creates an organic, often unpredictable surface. The variations can lead to mesmerizing effects that mimic natural phenomena think of autumn leaves or sunsets over a tranquil lake.
-
Emphasis on Form: This glaze beautifully complements sculptural shapes. The way it flows and pools accentuates the contours of the piece, inviting the viewer to appreciate the artistry from every angle.
-
A Connection to Tradition: Using this glaze connects me to a centuries-old practice, bridging ancient techniques with modern aesthetics. It’s as if each piece I create tells a story of its own, steeped in history yet brimming with contemporary relevance.
When working with this glaze, I recommend keeping an open mind and embracing the element of surprise. Every firing can yield unexpected results, leading to a delightful dance between intention and chance. Whether you’re an experienced ceramicist or just dipping your toes into this art form, exploring this glaze can add a rich layer of depth to your creations.
The Role of Kiln Temperature in Shino Results
Considering kiln temperatures, Shino is quite the unpredictable partner. One minute, it’s all about delicate, soft hues, and the next, it’s pushing bold, earthy tones that grab you by the collar. The magic, however, really lies in how hot you’re willing to let that kiln run.
You see, a low firing can lead to muted colors, almost like a whisper. But push the heat a little higher, and suddenly, you’re dealing with something much more expressive. There’s a sweet spot, though, where the balance of temperature creates surface variations that never fail to surprise me.
Of course, the atmosphere inside the kiln plays its own mischievous role. In reduction, the glaze develops those rich textures, breaking unpredictably in a way that reminds you that control is just an illusion in this process. It’s thrilling and, admittedly, frustrating at times.
Through my own countless firings, I’ve learned that even a degree or two can make all the difference. When you find that perfect temperature for your piece, it’s like discovering an unspoken language between you and the clay, one that you can’t rush but must coax gently.
Every time I open the kiln, it feels like Christmas morning. The results are never the same twice, and it’s that unpredictability that keeps me coming back, each time a little more curious about what the fire will reveal.
Preparing Your Clay for Shino Application
When preparing your clay for a Shino application, the groundwork matters. Let’s dive into what I’ve learned over time, not from books but hands-on practice. This stage is all about ensuring your clay body is primed to absorb that gorgeous glaze in just the right way.
First, you want to pay attention to your clay’s texture. A smooth and even surface is crucial, but don’t stress too much about perfection. Those tiny imperfections? They can give your piece character, especially once the glaze reacts with them. I usually burnish my clay lightly, but not too aggressively just enough to knock down the rough patches while leaving a natural feel.
Also, consider timing. If you apply the glaze when the clay is too dry, it’s like trying to paint a wall that’s already flaking. Aim for the right level of moisture. Leather-hard is ideal firm but still holding a bit of give. This allows the clay to absorb and bond with the glaze more effectively.
Before you start glazing, it’s worth taking the extra time to wipe down your pottery with a damp sponge. This removes dust, which can block the glaze from sticking. And trust me, a dusty surface will only leave you with inconsistent, patchy coverage.
Also, think about your clay’s composition. Porcelain and stoneware behave differently, and this will impact how the glaze settles. If you’re working with a groggy clay, expect some unpredictability, but that’s part of the charm, isn’t it?
Here’s a quick checklist before applying your Shino glaze:
- Ensure the surface is smooth but with character.
- Apply the glaze when the clay is leather-hard.
- Wipe the surface to remove dust.
- Consider your clay’s texture and composition for the best results.
Combining Shino with Other Glazing Techniques
When I first began experimenting with Shino, I quickly realized the real magic happens when you bring other glazing methods into the mix. The contrast between its rustic, velvety texture and the glassy brilliance of celadons or temmoku glazes is breathtaking. It’s like they’re having a conversation, each glaze telling its own story in tandem with the other.
Layering can get tricky, though. You need to know how these glazes interact with each other in the kiln, as some combinations can run or warp unexpectedly. It’s all about testing finding those beautiful accidents that make your piece sing. That’s when the real adventure begins, in those moments of unpredictability.
One technique I enjoy is to apply a thin layer of Shino over an underglaze or slip. It softens the colors underneath, allowing the base layer to peek through, creating a dreamlike haze. This can give an almost misty effect that’s subtle, but absolutely captivating.
Alternatively, you can pair Shino with a matte glaze. The textural difference alone makes the piece irresistible to the touch. When you bring them together, you’re working with both light and shadow, smooth and rough, making your pottery an experience, not just a visual piece.
The joy of combining techniques is that no two results are ever quite the same. You never know how the kiln will transform your work. That’s the thrill embracing the unknown and seeing what the fire gives you.
Best Practices for Layering Shino Glazes
As for layering Shino glazes, it’s all about experimentation and knowing how the glazes play off one another. I’ve found the real magic happens when you let yourself explore – because trust me, no two pieces are ever the same. Here are a few things to keep in mind:
-
Start with the right base: You want your first layer to be solid but not too thick. It’s easy to go overboard here, but less is more with that first coat. Whether it’s white or a more translucent base, keep it consistent.
-
Consider drying time: Before you even think about adding the next layer, give it time. Let the first coat dry until it feels almost leather-hard. If you’re impatient like I used to be, you’ll end up with uneven spots. Patience is key here.
-
Vary thickness and application technique: One of the most satisfying parts of layering is playing with how you apply each glaze. Try spattering, dipping, or even brushing your second layer in different spots. Each method adds its own flair, and that’s where personality shines through.
-
Temperature control: Shino responds dramatically to different firing conditions. I’ve found that layering with higher silica-content glazes beneath can create some stunning carbon trapping when fired in reduction. The top coat can melt into a wild, unpredictable texture.
-
Be ready for surprises: This is the fun part – you never quite know what’s going to come out of the kiln. Some layers will react, run, or even bubble up. That unpredictability is what keeps me coming back for more. It’s not about perfection, but about discovery.
So, as you layer and explore, remember – it’s not about controlling the process but partnering with it.
What People Ask
What makes a glaze a Shino glaze?
Shino glazes are traditional Japanese glazes that are known for their unique appearance, typically featuring a creamy white or orange surface with variations like carbon trapping, creating black spots or smoky textures. They are made primarily from feldspar, clay, and quartz. Shino glazes often produce a thick, soft texture that may range from glossy to matte. The glaze is also characterized by its ability to interact heavily with the clay body, emphasizing texture and giving each piece a unique finish.
Are Shino glazes food safe?
Shino glazes are generally considered food safe, especially when formulated and fired properly. However, there are exceptions. Some versions of Shino glazes that incorporate carbon trapping or other metallic elements may have surfaces that are less stable or may have small cracks, which could potentially harbor bacteria. It’s essential to ensure that the glaze has been tested for food safety and that it forms a durable, non-porous surface to prevent contamination.
How many coats of Shino glaze?
The number of coats of Shino glaze needed depends on the desired effect and the thickness of each application. Typically, potters apply two to three coats of Shino glaze to achieve an even coverage with its signature textures and color variations. Applying too few coats may result in an inconsistent finish, while too many coats can cause the glaze to pool or drip during firing. It’s important to apply the glaze evenly for the best results.
What colour is Shino glaze?
Shino glaze can range in color from creamy white to orange, red, or even black depending on the specific firing conditions and glaze formulation. Its white tones are often seen in traditional pieces, but modern interpretations, especially those that incorporate carbon trapping, can exhibit gray or black speckling. The color is also influenced by the clay body underneath the glaze, with richer, earthy tones emerging from darker clay bases.
What does Shino mean in pottery?
Shino in pottery refers to a style of glaze that originated in Japan during the late 16th century. The term ‘Shino’ is derived from the region in Japan where this type of glaze was first developed. The glaze was traditionally used on tea bowls and other ceramics, becoming highly regarded for its rustic, earthy beauty and unique surface textures. Today, Shino glazes are used globally and are admired for their distinct color variations and depth.
Can you use Shino glaze in an electric kiln?
Yes, Shino glaze can be fired in an electric kiln, although it is traditionally fired in gas or wood kilns, which often allow for more dramatic effects like carbon trapping and reduction firing. In electric kilns, you may not achieve the same level of variation or surface effects, but it is still possible to produce beautiful results. Many potters experiment with firing schedules in electric kilns to replicate the look of a reduction atmosphere as closely as possible.
Why are some pottery glazes not food safe?
Some pottery glazes are not food safe because they contain toxic materials like lead, cadmium, or barium that can leach into food or drink. Additionally, glazes that craze (develop fine cracks) or have unstable surfaces may also trap bacteria or contaminants. Glazes need to be fired to the correct temperature to vitrify properly and become non-porous. It’s essential to use glazes that are specifically tested and labeled as food safe to ensure they don’t pose a health risk.
What makes a Chun glaze?
Chun glaze, originally developed in China, is characterized by its translucent, often blue or pale green hues with a smooth, glossy surface. It is made from a high-silica glaze with a high alumina content, which gives it a unique opalescent quality. The glaze often has tiny bubbles or slight iridescence and can produce subtle variations in color depending on the thickness and firing conditions. Chun glazes are admired for their soft, elegant appearance and delicate tonal shifts.
Is glaze pottery at home food safe?
Glaze pottery made at home can be food safe, but it depends on the materials and firing conditions used. To ensure food safety, the glaze must be free of toxic ingredients, properly formulated, and fired to the correct temperature to form a smooth, non-porous surface. It’s recommended to use commercial glazes that are labeled as food safe and follow proper kiln-firing procedures. Additionally, testing the finished pottery for leaching or durability is a good practice before using it for food.
Your reflection on the enchanting world of Shino glaze resonates deeply with me! I remember my first experience watching pieces emerge from the kiln, each one uniquely beautiful, like a surprise gift. The way you describe the connection between the maker and their work captures the essence of ceramics perfectly. It’s almost meditative, waiting for that moment when the kiln door opens, revealing the unpredictable patterns and colors that emerge from the fire. I’ve found that every piece tells its own story, echoing the traditions and craftsmanship of those who came before us. The duality you mention how Shino can appear both soft and rugged truly reflects the complexities of life itself. It’s fascinating how a simple glaze can evoke such profound emotions and connections to nature. I wholeheartedly agree; every time I apply that glaze, I feel like I’m engaging in a beautiful dialogue with my materials. Thank you for sharing your journey and insights; it inspires me t
I couldn’t help but smile reading about your thrill as you dip your brush into that traditional glaze! It’s a sensation many artists understand so well. The way you describe the alchemical dance in the kiln is so poetic; it perfectly captures that moment of anticipation when you open the door and unveil your creations. I, too, love experimenting with layering glazes; it truly is like painting with a vibrant palette. Recently, I layered a deep blue with a translucent white, and the result was mesmerizing! The unexpected surprises that emerge during firing never cease to amaze me. I appreciate your perspective on the importance of patience in this art form. It’s that wait that builds excitement, like the suspense of a good novel. Your encouragement to explore the unknown resonates deeply with me. Each firing is an adventure, and I look forward to diving into this captivating world and discovering even more about my artistic voice. Thank you for sharing your insights
Your description of working with ceramics is so evocative! I can almost feel the clay in my hands as I read your words. I completely agree that there’s a unique magic in how glazes capture the essence of nature. The unpredictability you mentioned reminds me of the thrill I experienced when I first saw my work emerge from the kiln. It’s like unveiling a hidden treasure! Your insight about the beauty of imperfection truly resonates with me. I often find that my favorite pieces are the ones that didn’t turn out exactly as planned. The drips and runs you mentioned often add character and tell their own stories. I also love how you connected your first encounter with this glazing style to the surrounding landscapes what a beautiful metaphor! It’s moments like those that deepen our connection to our craft. I’m excited to continue experimenting and embrace that delightful chaos you spoke of. Your encouragement to let intuition guide the creative process is a fantastic reminder
I absolutely resonate with your experience of diving into Shino pottery! The charm of its variability is one of the most delightful aspects for me as well. Each piece feels like a unique story waiting to be told. I’ve experimented with different application techniques too, and it’s fascinating how a simple shift in technique can lead to an entirely new aesthetic. Recently, I created a bowl that had this unexpected burst of orange with a textured finish that felt like a soft sunset. It was such a thrill to unveil it! I also love the tip about experimenting with various clays I’ve found that mixing a stoneware body with Shino glaze creates a stunning contrast that brings out the glaze’s richness. Your mention of patience is spot on; it’s that waiting game between firing and reveal that keeps me coming back for more. Thanks for sharing your journey; it’s always inspiring to hear how others connect with this magical medium!