The Essentials of Print Picture on Material
Let’s dive into the essentials of mastering the art of ‘Print Picture on Material’. Whether you’re a hobbyist or someone experimenting with creativity, this process can be surprisingly rewarding. I’ve gone through the ups and downs myself, and let me tell you it’s not as tricky as it looks if you break it down into clear steps.
Understanding the Process
First, it’s all about picking the right material. Trust me, this makes or breaks the final product. For most cases, fabrics like cotton, canvas, or even polyester can work wonders. The key is to choose something with a smooth texture to ensure your picture doesn’t distort during printing.
Must-Have Tools for Success
- High-quality image: The clearer, the better. Blurry images won’t do justice to your material.
- Transfer paper: This acts as the medium between your design and the fabric. Make sure it’s compatible with the fabric you’ve chosen.
- Iron or heat press: A steady heat source will seal the design onto the material be sure to apply consistent pressure.
- Printer: It goes without saying, but not all printers are up for the task. An inkjet printer tends to work best for most fabrics.
Tips From My Experience
- Always pre-wash your fabric. This removes any factory coatings that might affect the final print.
- Test a small corner of the fabric before diving in. I’ve learned this the hard way avoid disappointment by testing early.
- Work in a well-ventilated space. You’ll be dealing with heat and some materials that might release fumes during the process.
And there you have it. With the right materials and a bit of patience, ‘Image transfer onto fabric’ becomes a fun, creative process that lets your personality shine on any fabric.
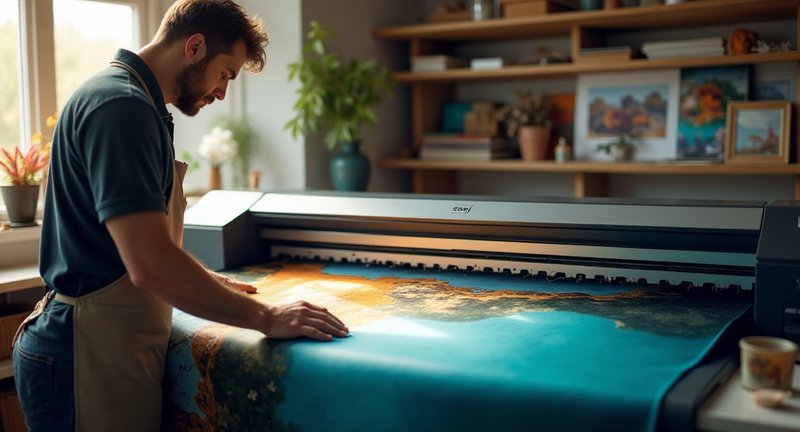
The Versatility of Print Picture on Material
You know, there’s something uniquely satisfying about seeing an image come alive on fabric. It’s not just about transferring a picture; it’s about giving it a new home. The texture of the material adds a layer of depth that you simply don’t get with traditional frames.
I’ve experimented with various surfaces, from soft cotton to rugged canvas. Each one transforms the design differently. A vibrant design on a smooth fabric can look almost like a painting, while on rougher textures, it feels more raw and dynamic.
What really fascinates me is how a single image can tell a different story depending on its backdrop. The material itself becomes part of the art, blending with the image to create something more tactile, more intimate.
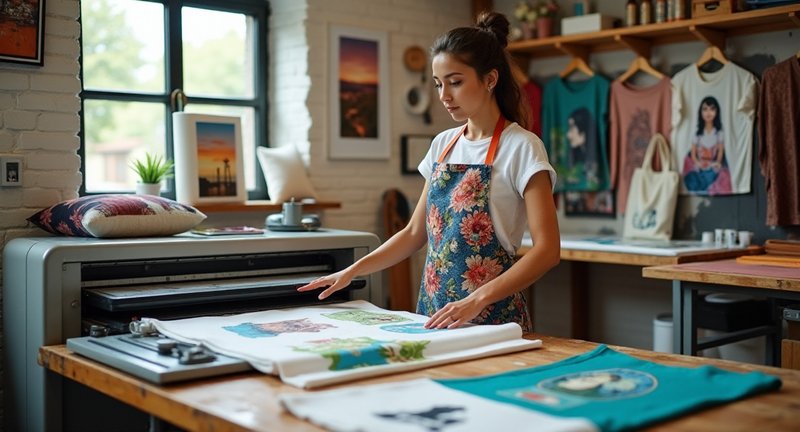
I’ve found that it’s a great way to add a personal touch to any space. There’s something special about a design that you can not only see but also feel. It’s like you’re bringing the art off the wall and into the room itself.
Whether it’s a favorite photo or an abstract design, the possibilities are endless. Each fabric holds the potential to enhance or even change the meaning of the image. It’s a playful process, one that keeps surprising me with every new creation.
Introduction to Printing Images on Fabric
When I first started experimenting with transferring designs onto fabric, it felt like opening a door to a whole new world of creativity. The idea that you could take an image, something digital or hand-drawn, and give it life on a soft, tactile surface seemed almost magical.
The process itself is surprisingly simple, yet filled with possibilities. From cotton to silk, each fabric offers its own character, influencing how the colors pop and how the texture plays with the final result. The key is in selecting the right material for the image you want to immortalize.
What I love most is the versatility. You can customize anything, from a quirky t-shirt to a decorative pillowcase, or even a unique piece of art to hang on the wall. Once you get the hang of it, you’ll never look at a plain piece of fabric the same way again.
I remember my first project an old tote bag that I transformed with a vibrant print. Watching the design fuse with the fabric was incredibly satisfying, and I’ve been hooked ever since. It’s more than just creating something visually appealing; it’s about infusing your personal touch into everyday items.
If you’ve never tried it, you’re missing out on a whole dimension of creative expression. Trust me, once you start, it’s hard to stop. It’s addictive in the best way possible!
Understanding Different Printing Techniques
In the matter of printing techniques, you’d be surprised at how many creative options exist beyond what we typically think of. I’ve dabbled in a few myself, and it’s fascinating to see how each method brings out something unique in a design. Let me share some of what I’ve learned along the way.
One of the most popular methods is screen printing. It’s a bit of a classic, especially if you’re looking to mass-produce designs. Essentially, a stencil is used to transfer ink onto your surface. What’s great about screen printing is the vibrant colors you can achieve, but be warned it works best with simpler designs and fewer colors.
For something a bit more high-tech, there’s sublimation printing. This method uses heat to infuse dye directly into the fabric (or other surfaces), making it a fantastic choice if you want long-lasting and detailed prints. I’ve tried this for some custom projects, and the results were stunning. It’s ideal for more intricate, colorful designs, but it only works on synthetic materials.
If you’re after a bit of texture, embossing is worth considering. Here, heat and pressure are used to create a raised design, giving your project a 3D effect. This technique is often used on paper, but I’ve seen it applied beautifully on fabrics and leather as well. It adds a tactile quality that screen printing or sublimation simply can’t match.
Here’s a quick comparison for you:
- Screen Printing: Bold, vibrant colors; best for simple designs.
- Sublimation: Detailed, durable prints; works on synthetic surfaces.
- Embossing: Raised, textured finish; adds a luxurious touch.
Each technique offers its own flavor of creativity. So, if you’re diving into this world, don’t be afraid to experiment your perfect print might be just one technique away.
Advantages of Fabric Printing Methods
Fabric printing opens up a world of creative possibilities. From personalizing a piece of clothing to crafting a one-of-a-kind home decor item, the methods are as diverse as the results. It’s more than just applying ink to fabric; it’s about creating something that resonates.
Each method comes with its own charm. Screen printing, for example, is ideal for bold, vibrant designs. I remember using it for a series of t-shirts once, and the colors just popped in a way that felt almost alive. This technique gives you control over every detail.
Digital printing, on the other hand, offers precision and variety. If you’ve ever tried to transfer a complex design with fine details, this method is your best bet. It’s like taking a high-definition photograph and placing it on fabric without losing any of its crispness.
Then there’s sublimation, a process that works like magic, embedding the design into the fabric rather than sitting on top of it. It’s a seamless, soft finish that you can barely feel when you touch the material. I still wear a scarf I printed this way feels like it’s been part of the fabric from the beginning.
What I’ve come to appreciate about fabric printing is that each method has a distinct personality. Whether you’re after durability, softness, or bright, bold colors, there’s a method to match your vision.
Preparing Your Material for Printing
Considering preparing your material for printing, it’s all about laying the right foundation. I’ve learned that the success of your final piece hinges on how well you set things up from the start.
The first thing I always do is inspect the material itself. Different textures and surfaces demand different approaches. Whether you’re working with fabric, wood, or even glass, each requires a specific treatment to ensure the ink holds up beautifully.
Next, I think about color. What looks vibrant on a screen may not translate as boldly on a textured surface. I recommend always adjusting your design for the tones of your material trust me, it’s better to tweak it now than to feel disappointed later.
Another thing I’ve picked up is to check the resolution. If your image isn’t crisp enough, it could end up looking dull or blurry once applied to the material. And nobody wants that. Go for higher DPI settings to avoid regret.
Oh, and don’t forget to preview your design in different sizes. I usually test the layout in both small and large formats because you never know how it might shift depending on the dimensions of the material.
As a matter of fact, take the time to clean the surface. Even the tiniest speck of dust can affect the final look. A well-prepared surface will give your printed design the sharpness and clarity it deserves.
Choosing the Right Printer for Fabric Applications
With respect to working with fabric, choosing the right printer is like picking the right paintbrush for a canvas. Not all printers are created equal, and trust me, I’ve learned this the hard way. You need a machine that can handle the texture, flexibility, and weight of fabric without losing its mind.
From my experience, inkjet printers are a solid option. They offer vibrant colors and soft finishes that won’t turn your fabric into a stiff board. But, don’t just grab any inkjet off the shelf. Look for ones that specify they’re compatible with fabric applications. I once used a standard printer, and let’s just say it didn’t end well.
Laser printers, on the other hand, bring sharpness and precision. If you’re going for intricate designs or text, they’re perfect. But be cautious laser prints can sometimes crack when stretched or washed, which might not work for every project.
If you’re serious about long-lasting prints, consider dye-sublimation printers. They’re a bit of an investment, but wow, do they deliver! The print bonds directly to the fabric fibers, so it’s not just sitting on top. It becomes part of the material. No fading, no peeling.
Also, don’t forget about the inks. Make sure they are fabric-friendly, like pigment-based or sublimation inks. I’ve found water-based inks to be pretty great for soft and flexible results.
Your fabric project deserves the right tools, and a good printer can make all the difference between ‘meh’ and ‘wow.’
Ink Types and Their Importance in Fabric Printing
With regard to fabric printing, one thing I’ve learned through trial and error is how crucial the type of ink can be. You might think ink is just ink, right? Well, not exactly. The kind of ink you choose can drastically affect not just how your design looks, but how long it lasts and how it feels on the fabric.
Let’s break it down:
-
Water-based inks: These are great for soft fabrics. The design almost feels like it’s part of the fabric itself. If you want to Print Picture on Material that needs to be breathable and soft, water-based inks are your go-to. They’re also eco-friendly, which is a win-win.
-
Plastisol inks: Now, if you’re aiming for bright and bold colors, especially on darker fabrics, Plastisol is your friend. It sits on top of the material, so the image really pops. The trade-off? It feels a bit heavier, which some people love and others not so much.
-
Discharge inks: These inks are like fabric wizards. They strip the color from the fabric and replace it with your design’s colors. Ideal for vintage looks. The best part? It leaves the fabric feeling soft and natural, like it was always meant to be that way.
Don’t overlook specialty inks, like metallic or glitter varieties, when you’re after that extra flair. They might be a bit tricky to work with, but the effect can be stunning, giving your fabric a unique, textured look that really stands out.
So, when you’re ready to Transfer image to fabric, take a moment to think about what you want from the end product. The right ink can make all the difference between a design that fades fast and one that stands the test of time.
Exploring Heat Transfer Techniques
When discussing working with different materials, one of the most exciting challenges I’ve faced is mastering heat transfer techniques. At first glance, it seems simple just apply heat, right? Well, not quite. There’s an entire science behind how heat moves through various surfaces and how it impacts the end result.
Let’s break down some key methods you might explore:
-
Sublimation Transfer: This is a fascinating technique where solid inks are transformed into gas without becoming liquid first. The trick? High temperatures and special surfaces, like polyester. What I love about sublimation is the vibrant colors it produces, almost as if the design becomes one with the material.
-
Heat Press Vinyl: For those who love working with textiles, heat press vinyl offers a quick and durable way to create custom designs. You cut the design out of vinyl, apply it to your fabric, and press with heat. I’ve had a lot of fun experimenting with different vinyl textures glitter, metallic, you name it!
-
Direct-to-Film (DTF) Printing: This relatively new method caught my attention because of its versatility. It works on a wider range of fabrics and produces vibrant results, even on darker materials. You simply transfer the ink from film to fabric with heat and pressure.
Every method has its quirks. For instance, getting the right temperature is crucial you don’t want your design melting into a mess! And don’t get me started on pressure, which needs to be just right for even, crisp edges. Experimenting is key, and trust me, you’ll get hooked once you start!
Print Picture on Material: An In-Depth Look
Working with different fabrics to bring an image to life feels almost like creating a magic spell. The texture, the colors, and the entire process transform a blank canvas into something memorable. You’re not just adding a picture, you’re making it part of the material’s soul.
One of the most exciting things about this is the versatility of materials you can experiment with. Cotton? Great for crisp, bold designs. Silk? It gives your image an ethereal, almost floating quality. Every material tells a different story through the print.
I’ve always found that paying attention to the interaction between the ink and the fabric’s texture is crucial. That little bump or weave pattern you may not notice at first glance? It can drastically affect how the image stands out or fades into the background.
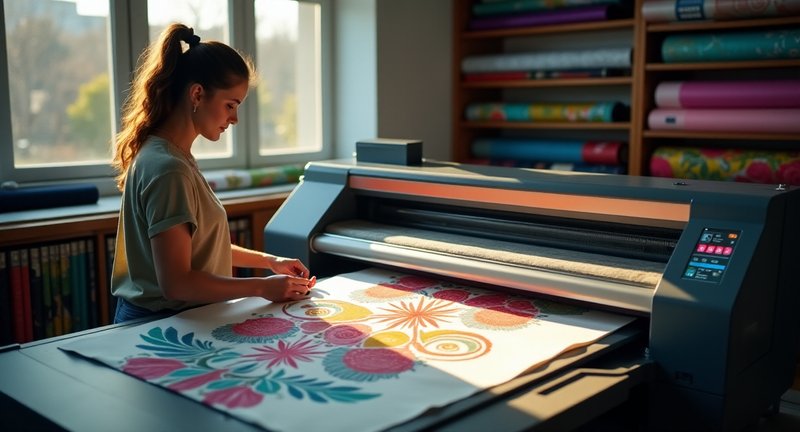
Choosing the right method, whether it’s sublimation, screen printing, or even heat transfer, isn’t just a technical decision it’s an artistic one. It can change how vibrant or subtle your image turns out, and there’s real beauty in getting that just right.
To me, the real reward comes when you run your hand over the final product. The texture of the material combined with the printed image creates a tactile experience that’s as satisfying as the visual one. It’s like holding a piece of art that feels alive.
The Screen Printing Process Explained
When I first stumbled upon screen printing, I was immediately captivated by its artistry. The process is a beautiful blend of science and creativity, almost like magic unfolding before your eyes.
It all starts with a mesh screen, which acts as the canvas for your designs. Picture this: the screen is stretched taut, and then a special emulsion is applied, creating a delicate dance of light and shadow.
Once the emulsion dries, you’ll place your design on top and expose it to light. The areas that are touched by light harden, while the untouched parts wash away, revealing your unique pattern. This step feels like unveiling a hidden treasure, and I often find myself in awe of what appears.
Next comes the ink, which is pushed through the mesh using a squeegee. It’s a satisfying motion, like spreading frosting on a cake. As the ink seeps through, I can’t help but admire the vibrant colors that burst forth, bringing my design to life.
After printing, the piece needs to cure, which can involve heat. This step ensures that the design becomes an integral part of the fabric. There’s something incredibly fulfilling about watching a flat piece of cloth transform into a work of art.
Every layer added brings me one step closer to the final product, and I can hardly contain my excitement. In the end, you’re left with a striking piece that tells a story, reflecting your unique vision.
Direct-to-Garment (DTG) Printing: A Modern Approach
Direct-to-Garment (DTG) printing has truly revolutionized the world of custom apparel. When I first encountered this modern technique, I was amazed at its ability to transform a simple garment into a canvas of artistic expression. Unlike traditional methods, DTG allows for vibrant, intricate designs that practically leap off the fabric. It feels like magic when you witness how a digital image is translated directly onto clothing.
Here’s what I love most about DTG printing:
-
Unlimited Design Potential: Whether you’re working with a complex artwork or a simple logo, the sky’s the limit. The detail achieved is astounding, allowing for photo-realistic images that make each piece unique.
-
Eco-Friendly Options: Many DTG printers utilize water-based inks, which means you can create stunning designs without feeling guilty about harming the environment. This sustainable approach is something I proudly support.
-
No Minimum Orders: Gone are the days of ordering dozens of items just to get a few customized pieces. With DTG, I can create a single, bespoke shirt or hoodie, which is perfect for special occasions or personal gifts.
-
Quick Turnaround: When I need something done fast, DTG printing saves the day. The process is efficient, enabling me to receive my custom pieces in no time at all.
-
Soft Feel: One of my favorite aspects is how the ink merges with the fabric, giving the finished product a soft, comfortable feel. It’s like wearing a work of art!
In my experience, DTG printing not only fulfills creative visions but also opens doors to endless possibilities in the point of personal expression. If you’re looking to make a statement, this is undoubtedly the way to go!
Using Sublimation for Vibrant Prints
Sublimation has revolutionized the way I approach creating bold, vivid designs. It’s like unlocking a new level of creative freedom. The beauty of sublimation lies in how it blends colors seamlessly into the fabric or item you’re working on, with no heavy textures or layers.
You simply start with a special type of ink and transform your design onto the desired surface with heat and pressure. The process feels almost like magic, watching those colors sink into the material, becoming part of it, rather than sitting on top.
In my experience, the results are vibrant and last longer than traditional methods. I’ve tried various techniques before, but sublimation adds a unique clarity and brilliance that’s hard to achieve with other methods.
One of the best parts? The versatility. Whether you’re working with apparel, mugs, or home decor items, the results are consistently striking. And the colors remain bold wash after wash, time after time.
It’s satisfying to see your ideas transferred onto something that looks professional and lasts. It’s a perfect combination of art and science, where creativity meets technology in the most exciting way. You just need the right tools and a bit of patience, and the outcome is worth every moment.
Essential Tools for DIY Fabric Printing
Let’s dive into the essentials you’ll need for a successful DIY fabric printing project. From my experience, having the right tools on hand can really make or break the process. It’s not just about having materials; it’s about knowing how to use them to bring your creative vision to life.
-
Fabric Paint or Ink: The cornerstone of any fabric printing project. It’s important to pick the right type for your fabric. Some inks work best on cotton, while others are designed for synthetic materials. Be adventurous with color, but remember to choose something that can hold up against washes.
-
Blank Fabric: You’ll need to pick the right canvas for your project, so to speak. Cotton is a popular choice, but linen or even canvas can give your project a different texture. I like to experiment with different fabrics just to see how the prints react.
-
Stencil or Stamp: If you’re not the freehand type, stencils and stamps are your best friends. You can either buy pre-made designs or carve your own from linoleum blocks or even potatoes (seriously, potato stamps bring a whimsical touch to any project).
-
Squeegee or Brayer: For spreading ink evenly, these tools are invaluable. The squeegee is your go-to for screen printing, and a brayer (which is basically a roller) works wonders for block printing.
-
Heat Source: After applying your design, you’ll need to heat-set it. This ensures the ink doesn’t fade or wash away. A regular iron usually does the trick, but a heat press will give you more consistent results.
-
Protective Gear: Don’t forget gloves and aprons! Trust me, fabric ink has a way of finding its way onto your clothes if you’re not careful.
Once you’ve gathered your tools, you’ll be ready to start experimenting and creating unique fabric designs. The fun part is seeing how each tool plays a role in the final masterpiece. Happy crafting!
Tips for Achieving Quality Prints
When dealing with getting that perfect print, it’s often the little details that make the biggest impact. Before diving into the process, always think about the texture and quality of the surface you’re working with some canvases just love soaking up color, while others can be a bit temperamental.
One tip I always keep in mind is to consider the lighting where the piece will eventually live. Natural light can bring out hues you didn’t expect, while harsh, artificial light can sometimes dull your masterpiece. It’s like crafting with an audience that you can’t see.
Also, don’t overlook the importance of experimenting with test prints. Trust me, even the pros sneak in a few trials before committing to the final run. There’s something almost magical about seeing the first attempt, even if it’s not perfect it’s part of the journey.
Another overlooked aspect is letting the ink set properly. We all know the temptation to rush, but giving your work that extra time to breathe and settle can be the difference between ‘okay’ and ‘wow!’ So resist the urge to touch too soon.
As a matter of fact, always take a step back once you’ve finished. Sometimes the details you missed while up close reveal themselves when viewed from a distance. The wider perspective gives you a true sense of your finished piece, like a painter admiring their completed canvas from across the room.
Questions and Answers
Can I print a photo on fabric?
Yes, you can print a photo on fabric using various methods such as direct printing with a specialized fabric printer, iron-on transfers, or even fabric sheets designed for inkjet printers. These techniques make it possible to personalize items like clothing, pillows, or quilts with your favorite images. Printing on fabric has become increasingly popular for both crafting projects and personalized gifts, offering a durable and creative way to showcase your photos.
How do you print onto fabric?
Printing onto fabric involves selecting the right method and materials for your project. One popular option is using fabric sheets that are compatible with inkjet printers. Simply print the photo onto the fabric sheet, and once it’s ready, you can sew or attach it to your desired item. Another option is to use an iron-on transfer. For larger or professional projects, fabric printers that directly print onto textiles can be used. The key is to ensure the fabric is pre-treated for printing to avoid issues like bleeding or fading.
How do I print a picture onto clothing?
To print a picture onto clothing, the most common approach is to use iron-on transfer paper. You can print your image on the transfer paper using an inkjet or laser printer, then use heat (with an iron or heat press) to transfer the image onto the fabric. Make sure the fabric is clean and smooth before applying the transfer. For long-lasting results, you can also opt for professional services that use methods like screen printing or direct-to-garment printing, which are particularly effective for custom apparel.
What is the best material to print a photo on?
Cotton is often considered the best material to print a photo on because it absorbs ink well and results in vibrant, clear images. Blended fabrics like cotton-polyester blends also work well, offering durability with good color retention. For professional projects, canvas is another excellent choice, providing a textured, artistic finish. The type of material you choose largely depends on your project’s purpose, whether it’s for a soft, wearable item or a decorative piece.
Does Shutterfly print photos on fabric?
Yes, Shutterfly offers services that allow you to print photos on fabric. You can choose from a variety of personalized items, such as photo blankets, pillows, and even tote bags. Shutterfly uses high-quality printing techniques to ensure that your images are sharp and vibrant on fabric. These custom fabric products make for meaningful gifts or unique home decor pieces, featuring your favorite moments or designs.
Can I print on fabric with a normal printer?
You can print on fabric with a normal inkjet printer by using fabric sheets designed for inkjet printing. These fabric sheets are specially treated to accept ink and can easily be fed through your printer. Another option is to use iron-on transfer paper, which allows you to print your image on paper and then transfer it onto fabric using heat. However, printing directly onto fabric with a regular printer is not recommended unless it’s specifically designed for that purpose.
What type of printer prints on fabric?
Specialized printers, such as fabric printers or direct-to-garment (DTG) printers, are designed specifically for printing on fabric. These printers use textile-friendly inks that bond with the fabric fibers, ensuring high-quality, durable prints. Inkjet printers can also print on fabric if you use fabric sheets or iron-on transfer paper. If you’re printing frequently or for commercial purposes, investing in a fabric printer is ideal for more detailed and professional results.
What is printing on fabric called?
Printing on fabric is generally referred to as ‘textile printing’ or ‘fabric printing.’ There are several specific methods, including digital fabric printing, screen printing, and direct-to-garment (DTG) printing. Each method offers different advantages depending on the fabric type, the design complexity, and the intended use of the printed fabric. Textile printing has a wide range of applications, from fashion and home decor to promotional products and art projects.
Can digital printing be done on fabric?
Yes, digital printing can be done on fabric using specialized digital fabric printers. Digital printing involves transferring an image directly onto the fabric using textile inks that bond to the fibers. This method allows for high-quality prints with intricate details and vibrant colors. Digital printing is highly versatile and can be used on various fabrics, making it ideal for producing custom designs, small runs of clothing, or personalized home textiles.
What are the methods of printing images on fabric?
There are several methods to print images on fabric, including screen printing, digital printing, direct-to-garment (DTG) printing, heat transfer (iron-on) printing, and dye sublimation. Screen printing is ideal for larger quantities, while digital and DTG printing are more suitable for detailed designs and small runs. Iron-on transfer printing is perfect for DIY projects. Each method has its own advantages depending on the type of fabric and the complexity of the image.
Which printer prints on fabric?
Direct-to-garment (DTG) printers and specialized textile printers are designed to print directly on fabric, using inks that are formulated for textiles. Some inkjet printers can also print on fabric, but they require the use of fabric sheets that are pre-treated for inkjet printing. For large-scale production or professional projects, using a dedicated fabric printer is recommended for high-quality and durable prints.
Can you get a picture printed on a shirt?
Yes, you can easily get a picture printed on a shirt using several methods. One popular method is to use iron-on transfer paper, which allows you to transfer a printed image onto the shirt with heat. For more durable and professional results, direct-to-garment (DTG) printing or screen printing are excellent options. Many companies also offer custom t-shirt printing services, where you can upload your image, choose your shirt type, and have it printed professionally.
I absolutely agree that picking the right printer is a game-changer when it comes to fabric projects! I learned that lesson too when I started experimenting with different types of printers for my fabric designs. My first attempt with a regular office inkjet left my fabric stiff and just not what I had envisioned. It was such a letdown. But when I finally invested in a printer that could handle fabric, the difference was night and day!
You nailed it with the importance of preparation! I learned the hard way how crucial it is to consider the material and color before printing. There was this one time I didn’t account for the texture of the fabric, and my design looked duller than I expected. Adjusting for the material’s tones is such a game-changer, especially when you want those vibrant colors to come through. And yes, resolution is everything! I’ve regretted not upping my DPI settings in the past never again! Also, cleaning the surface before printing? Totally agree, even the smallest details can make a huge difference. Great tips all around!
I can totally relate to your experience with fabric printing! I remember doing a custom batch of t-shirts with screen printing, and you’re right the colors almost jump off the fabric. There’s something so satisfying about seeing your design come to life like that. I’ve also tried digital printing for more intricate designs, and it’s a game changer! You get all the fine details, just as if they were right off a computer screen. But I’ve never tried sublimation printing I love the sound of how the design becomes part of the fabric. That scarf you printed must look amazing. Definitely going to give that a shot!
I love how you’ve broken down the different printing techniques here! Screen printing is definitely a classic, and it’s great for those bold, simple designs. I’ve tried it myself on some posters, and the colors really do pop! Sublimation is super intriguing too, especially for more detailed work. I’ve never done it personally, but I’ve seen the results on fabric, and it’s like the design is part of the material itself. Embossing though that’s on my to-try list! There’s something about that raised texture that makes everything feel more premium. Thanks for the great breakdown; you’ve inspired me to experiment!
Wow, your journey into fabric printing is so relatable! I felt the same thrill when I first tried it. There’s something magical about transforming a digital image into a tangible piece of art. The way you’ve described the personality of different fabrics resonates with me, especially when you mentioned how it can influence the colors and textures. I remember making a funky pillowcase with an abstract print, and it turned my living space into a vibrant gallery! It’s so satisfying to see your creative vision come to life. The versatility you highlighted is what makes this craft addictive it’s like you unlock a new level of creativity with each project. I can’t help but dive into new ideas every time I see a plain fabric! If anyone’s hesitant, I say just go for it; you won’t regret it. Keep sharing your amazing experiences!
Your insights about how different fabrics can alter the story of an image are fantastic! I totally resonate with that feeling of satisfaction when you see your design come to life. It’s like each piece of fabric adds its own narrative to the art, making it a more immersive experience. I once did a vibrant print on a rough canvas, and it felt so rugged yet artistic almost like a piece of street art! It’s such a great way to bring personal touches into our homes. The idea that we can merge art and tactile experiences is something I cherish. Plus, I love how you pointed out that the possibilities are endless. I’ve started exploring with different patterns and themes, and it’s like every new project opens up a whole new realm of creativity. Keep inspiring us with your wonderful ideas!
I absolutely love how you’ve captured the essence of printing images on fabric! I remember when I first tried this, I was amazed at how much of a difference the material choice made. For my first project, I went with a soft cotton, thinking it would be simple, but the texture gave my design an unexpected depth! And yes, pre-washing the fabric is a game changer. It really does help in avoiding any hiccups during the transfer. Your tips on using transfer paper and testing a small corner are spot on! It can be so disheartening to mess up a large piece, so that little test goes a long way. I’m excited to try out the heat press method next; it sounds like it could streamline the process even further. Can’t wait to experiment with new designs! Thanks for sharing such valuable insights!