The Basics of Leather Punching Tool
When I first grasped the world of leather crafting, the Leather Punching Tool quickly became my trusted companion. This nifty gadget is essential for creating those precise holes that make your leather projects shine.
Using a leather punch is like wielding a magic wand; it transforms a flat piece of leather into a canvas for creativity. Whether you’re adding rivets, laces, or just making holes for stitching, this tool is your best friend.
One of my favorite aspects of the Leather hole puncher is its versatility. You can choose from various sizes of punches, which means you can adapt to any project that comes your way. From delicate straps to hefty belts, there’s a punch for everything.
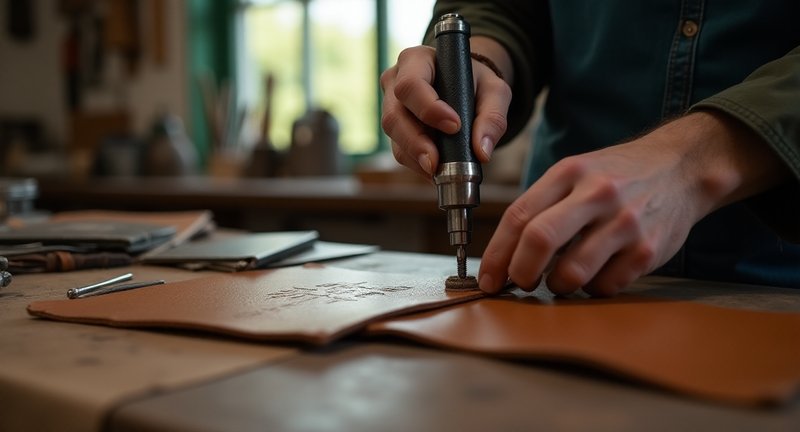
I remember the first time I used it on a wallet project. With each punch, I felt like an artist chiseling away at marble, revealing the beauty within. It’s incredibly satisfying to see your hard work come together with the precision of a well-placed hole.
Don’t be afraid to experiment with your Leather perforating tool! Each project is a new adventure, and every hole is a step closer to bringing your vision to life. Trust me, once you start punching, you’ll be hooked.
So grab that tool, unleash your creativity, and let your leatherwork flourish. You’ll be amazed at what you can create with just a little punch here and there.
How to Use a Leather Punching Tool Like a Pro
When I first ventured into the world of leather crafting, I quickly discovered the magic of precision tools. Among them, there’s one that stands out for its ability to elevate your projects to a whole new level. Knowing how to wield this tool like a pro can make a significant difference in the quality of your work. Here’s how I mastered it:
-
Choose the Right Spot: Always start by selecting a sturdy surface. I prefer using a cutting mat or a piece of scrap wood. It absorbs impact, ensuring a clean punch every time.
-
Mark Your Design: Before diving in, take a moment to sketch your design on the leather. This visual roadmap will guide your punches and keep everything aligned.
-
Test First: I can’t stress this enough! Always practice on a scrap piece of leather. This way, you can gauge the pressure needed and refine your technique without the fear of ruining your main piece.
-
Apply Even Pressure: When you’re ready to punch, grip the tool firmly and press down evenly. Uneven pressure can lead to jagged holes that can ruin your project. Trust me; it’s worth the extra second to get it right.
-
Keep it Clean: After a few punches, debris can build up. Give the tool a quick clean to maintain sharpness and efficiency. A little care goes a long way!
By integrating these steps into your crafting routine, you’ll not only become more adept at using this nifty gadget but also enhance the overall quality of your leather creations. Remember, practice makes perfect, and before you know it, you’ll be creating professional-looking items with ease!
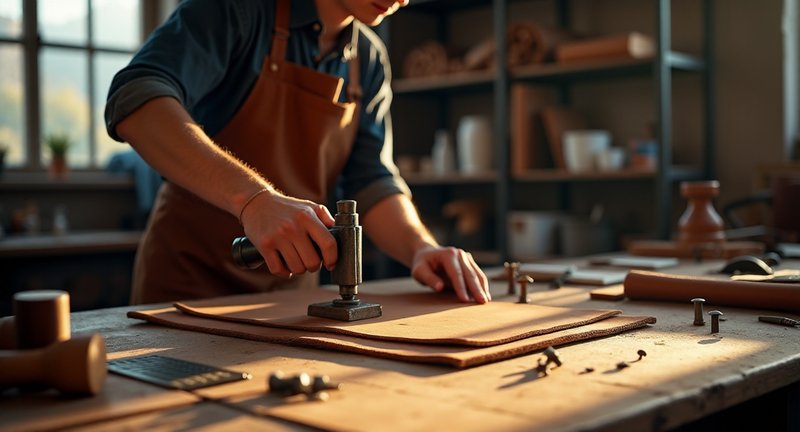
Types of Leather Hole Makers
When diving into the point of crafting with leather, understanding the various types of hole makers can be an adventure in itself. Each tool brings its unique flair to the table, allowing you to create with precision and style.
One of my favorites is the revolving punch. This beauty features multiple sizes in one handy device, making it a chameleon for any project. You can effortlessly switch between different hole sizes, which is a lifesaver when working on intricate designs. I’ve found it perfect for both thick and thin leather, effortlessly gliding through without breaking a sweat.
Then there’s the single-hole punch, a straightforward yet essential companion. It’s like that trusty friend who’s always there when you need them. This tool provides a clean, crisp hole that’s ideal for laces or small rivets, ensuring that every detail shines through. I often reach for this when I want to add a simple touch that packs a punch.
Let’s not forget about the chisel punch. This one is more than just a pretty face; it creates multiple holes in a single swoop, making it a favorite for those larger projects. I love using it when crafting belts or bags, where uniformity is key. The clean lines it leaves behind are nothing short of satisfying.
In my experience, exploring these tools can transform your leatherwork from mundane to magnificent. Each type has its personality, offering unique ways to express your creativity. So, if you’re embarking on your leather crafting journey, keep these tools in mind they might just become your new best friends.
Key Features to Look For
When embarking on your quest for the perfect tool for crafting, whether it’s for fashioning belts, bags, or other leather projects, there are several key features I’ve learned to prioritize from my own adventures in this vibrant hobby. Let’s dive into what makes a quality instrument truly stand out.
1. Adjustability:
A versatile tool can save you a lot of hassle. Look for options with adjustable settings, allowing you to create various hole sizes. This flexibility means you can adapt to different projects without needing multiple tools.
2. Ergonomic Design:
Comfort matters! An ergonomically designed handle reduces strain during those long crafting sessions. I’ve found that a well-placed grip can turn tedious work into a breeze.
3. Material Quality:
Not all tools are created equal. Check for high-quality materials, such as hardened steel, which will stand the test of time. You want something durable that won’t bend or break when you’re deep in a project.
4. Ease of Use:
Simplicity is key. The best tools feature intuitive mechanisms that make them user-friendly, especially for beginners. A straightforward design will make your crafting experience enjoyable rather than frustrating.
5. Portability:
If you’re like me and love to take your hobbies on the go, consider the tool’s portability. A lightweight option that fits neatly into a crafting bag is a game-changer for those spontaneous creative moments.
As you embark on your crafting journey, keep these features in mind. Trust me, they’ll make all the difference as you create your masterpieces!
The Importance of Hole Size
As for crafting, understanding hole size can be a game changer. I’ve spent countless hours creating beautiful projects, and it’s often the small details that truly elevate the final product. The size of the hole can dramatically influence both aesthetics and functionality.
Imagine trying to thread a delicate cord through a gaping hole. It feels like trying to fit a giraffe into a VW Bug completely impractical! On the other hand, a hole that’s too small can lead to frustration, as you wrestle with the material. It’s all about finding that sweet spot, the Goldilocks zone, if you will.
In my experience, experimenting with different sizes has led to some unexpected delights. I once stumbled upon a perfect combination while making a leather wallet. The right hole size allowed for seamless stitching, resulting in a sturdy yet elegant finish. It was like discovering a secret recipe that just clicks.
Moreover, don’t underestimate the aesthetic appeal of the right hole size. Whether you’re creating jewelry or customizing bags, a thoughtfully placed hole can add a unique flair. It draws the eye and invites curiosity, like a little window into your creative soul.
I always encourage fellow crafters to embrace their adventurous side. Play with different sizes and see how they transform your projects. You might be surprised by the doors (or holes) that open up when you step outside your comfort zone.
Material Matters: Steel vs. Brass
Considering the tools of our trade, material choice can make or break the experience, and nothing epitomizes this more than the age-old debate of steel versus brass. As someone who has dabbled extensively in crafting, I can tell you that both materials bring their own flair to the table, shaping not just the functionality of the tool but also the joy of using it.
Steel: The Stalwart Workhorse
Steel tools are the steadfast companions of serious hobbyists. Here’s why I gravitate toward steel:
- Durability: Steel is known for its toughness. If you’re looking for longevity, steel is your knight in shining armor.
- Precision: The rigidity of steel allows for fine, precise work. Perfect for those intricate projects that require a delicate touch.
- Cost-Effective: Generally, steel tools come at a more affordable price point, making them accessible for all hobbyists.
Brass: The Elegant Alternative
On the flip side, brass tools have a charm that’s hard to resist. Here’s what draws me to brass:
- Aesthetic Appeal: Brass has a warm, golden hue that’s undeniably attractive. It adds a touch of elegance to your workspace.
- Gentle on Materials: Brass is softer than steel, which means it’s less likely to damage delicate materials. This makes it ideal for intricate designs.
- Corrosion Resistance: Brass does well against the elements, making it a great choice for outdoor projects.
In the end, the choice between steel and brass tools boils down to personal preference and the specific project at hand. Whether you favor the brute strength of steel or the refined beauty of brass, both materials offer unique benefits that can elevate your crafting game. So, take a moment to consider what resonates with your style your creations will thank you for it!
How to Choose the Right Tool for Your Project
Choosing the right tool for your project is like selecting the perfect partner for a dance. It’s not just about the tool itself, but how well it complements your vision.
I remember my first crafting adventure, staring blankly at a wall of options. My instincts told me to reach for the shiniest one, but experience taught me that it’s not the glimmer that counts; it’s the functionality and fit for your specific needs.
Before diving in, take a moment to consider the materials you’ll be working with. Each project has its own personality, and your tools should harmonize with that character. For instance, if you’re working with delicate fabrics, a gentle touch is key.
I also find it invaluable to reflect on the complexity of your design. If your project requires precision, then a more specialized tool can make all the difference. The right choice can turn frustration into satisfaction, transforming a laborious task into an enjoyable experience.
Don’t forget to consider your comfort and grip. A tool that feels like an extension of your hand can elevate your crafting to new heights. I’ve had my fair share of sore fingers from ill-fitting tools, and trust me, it’s a lesson learned!
Also, never underestimate the power of recommendations. Seek out experienced crafters who can share their wisdom. You’ll discover that tools often carry stories, and those tales can guide you toward your best choice.
So, next time you’re faced with a myriad of options, remember: choose wisely, and let your creativity flow with ease.
Essential Accessories for Leather Punching
When you’re diving into the craft of working with leather, there are a few key accessories that truly elevate the experience. It’s not just about making holes; it’s about doing so with precision, style, and a bit of flair. Trust me, I’ve learned this through a fair amount of trial and error.
First off, a good cutting mat is essential. Without it, you risk damaging your workspace, and let’s be honest, nobody wants to wreck their dining room table for the sake of a hobby. A self-healing mat makes the process smoother and keeps your tools in better condition.
You’ll also want to have a set of high-quality chisels. They’re often overlooked but having them around can make a world of difference, especially when you’re working on more complex patterns. Their sharpness and accuracy reduce the strain on your hands, making long sessions more enjoyable.
Marking pens or pencils tailored for leather are a must. They help outline your work before you commit to punching, allowing you to visualize the finished product and avoid mistakes. It’s a small step that saves you a lot of headaches down the road.
Also, a mallet specifically designed for leatherwork is non-negotiable. Wooden or rawhide mallets prevent unnecessary damage to your tools, extending their lifespan and helping you punch more evenly. It’s one of those items you don’t think you need until you try it then you wonder how you ever worked without it.
Step-by-Step Guide to Using a Hole Punch
Let’s dive into using a hole punch the right way because there’s a bit more to it than just squeezing handles. First, I always make sure to have my Leather Punching Tool in hand. It’s crucial to pick the right size, as one size definitely doesn’t fit all when it comes to making clean holes.
Before you press down, mark where you want the hole. You don’t want any guesswork here. I usually eyeball it, but feel free to grab a ruler if you’re aiming for perfection. Precision is key!
Now, the moment of truth squeeze. I prefer to apply steady, even pressure. I’ve learned over time that rushing this step can lead to a sloppy result. Let the Leather hole punch do the heavy lifting for you.
One tip I wish I knew earlier: punch into a soft surface, like a cutting mat. This gives the tool something to press against and protects your workbench. It’s a little detail that makes a world of difference.
Also, don’t forget to check your hole. A clean punch will have no frayed edges or awkward shapes. If it’s not perfect, adjust your grip or pressure and try again. There’s a satisfaction in getting that crisp, precise hole.
Tips for Maintaining Your Punching Tool
From my experience, keeping your punching tool in top shape isn’t as hard as it might seem. In fact, it’s one of those habits that pay off in the long run. Let’s dive into a few ways to ensure your tool lasts for years, maybe even outlives your need for it.
-
Keep it Sharp: The business end of your punching tool is all about precision. When the edges dull, you’ll start to notice ragged holes or, worse, uneven punches. Grab a small sharpening stone or fine-grit sandpaper to bring the edge back to life every now and then.
-
Clean After Every Use: No, seriously, don’t skip this. Leather fragments or dust from other materials can clog up your tool, leading to inconsistent results. A simple wipe down with a dry cloth is usually enough. If you’ve been working with something sticky, a bit of rubbing alcohol on a cotton swab will do wonders.
-
Oil It Up: Moving parts can get stiff over time. I recommend applying a drop of light machine oil to any joints or hinges. Don’t go overboard; a little goes a long way. This prevents rust and keeps your tool’s movement smooth as butter.
-
Store It Properly: Leaving it lying around in a drawer or toolbox? Not ideal. Store it in a dry place, ideally wrapped in a cloth or protective case. If you’re in a humid area, consider adding a packet of silica gel to prevent moisture buildup.
-
Check for Wear and Tear: Every so often, inspect the tool for any cracks, chips, or bent parts. Catching these early means less headache later.
Taking a few minutes to maintain your punching tool will make all the difference in your crafting journey. Trust me future you will thank you for it.
Common Mistakes to Avoid
When diving into any craft, especially leatherworking, it’s easy to get swept up in enthusiasm and overlook a few essential details. Trust me, I’ve been there. One mistake I’ve seen over and over is rushing the process. Leather demands patience if you rush, you’re likely to end up with uneven cuts or poorly finished edges.
Another common blunder is neglecting to properly mark out your pattern before making any cuts or holes. I know it’s tempting to just ‘eyeball’ it, but leather can be unforgiving. You can’t undo a misplaced hole.
Using the wrong tools for the job is also a frequent misstep. You might think you can get by with standard household items, but leatherwork requires specialized tools for a reason. Skimping on this will only lead to frustration down the line. Speaking of tools, always ensure they’re sharp. Dull tools can damage your material and leave you wondering why things aren’t turning out as expected.
Also, don’t forget about your workspace. A cluttered or unstable surface can lead to accidents or misaligned punches. A solid, clean surface is as important as the tools in your hand.
Avoid these pitfalls, and you’ll find your leather projects coming together with more precision and less headache. After all, half the joy is in getting the details right.
Crafting Projects That Benefit from Hole Punching
There’s something oddly satisfying about creating that perfect hole in a material with precision. Over the years, I’ve found many crafting projects that truly come to life once you introduce a little hole-punching into the mix. Whether you’re working with paper, fabric, or even tougher materials, those small, clean perforations can turn a simple idea into a polished masterpiece.
One of my favorite uses is in scrapbooking. Carefully punched holes give that rustic, yet refined touch to handmade tags, photo frames, or even layered embellishments. I love using this technique to bind small handmade notebooks or journals. It’s such an easy yet effective way to hold everything together while keeping a creative edge.
Moving onto more durable materials, I’ve experimented with felt and thin rubber sheets for custom coasters. Punching intricate patterns through these surfaces adds not only a visual element but also a textural twist. It’s like adding your own unique signature to everyday objects, all with just a few deliberate holes.
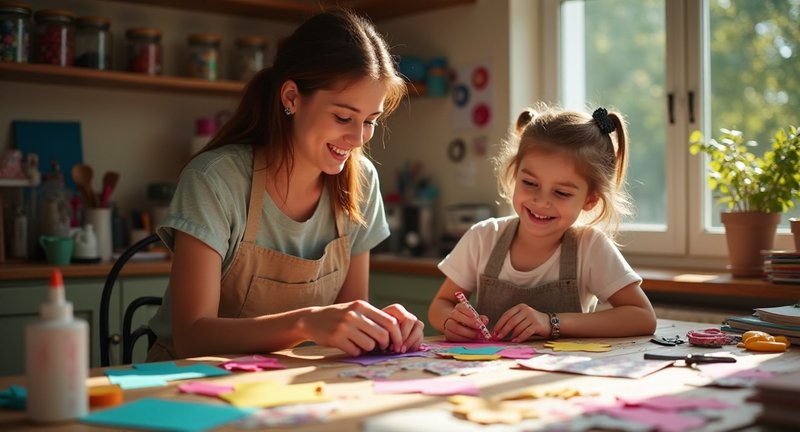
Jewelry-making is another realm where hole-punching shines. Creating custom charms or pendants from metal sheets or sturdy fabric brings out a lot of personality in your designs. Imagine making a pair of statement earrings with bold cut-outs or delicate bracelets that play with negative space.
When I work with leather, I find that adding perfectly spaced holes helps lace in decorative threads or add functional elements like buckles and rivets. These small, intentional punctures allow you to truly customize your project, transforming raw materials into something both practical and beautiful.
Understanding Leather Punching Tools
Let’s talk about the tools that make clean, precise holes in leather a game changer for any leather project. If you’ve ever tried to force your way through thick leather without the right tool, you’ll know that frustration firsthand. There’s an undeniable satisfaction in using something perfectly designed to do the job.
These tools come in all shapes and sizes, but the key is in selecting the right one for the task at hand. The size of the hole you need, the thickness of the leather, and the precision required all play a part. Sometimes, it feels like a balancing act, finding the sweet spot between force and finesse.
I remember the first time I used a handheld punch. There was a moment of realization this was far easier than I had anticipated. You align it, apply pressure, and just like that, a neat little hole appears. It’s a small victory, but a significant one when you’re crafting something by hand.
Rotary models, which resemble pliers, offer a variety of hole sizes in one tool, making them versatile for most projects. For those who like options, it’s a dream come true. But for projects that demand precision, a single-hole punch with an interchangeable tip might be your best friend.
Whatever option you choose, mastering these tools is essential for anyone who loves working with leather. It’s one of those small skills that makes a huge difference in the end result. Trust me, once you’ve used the right one, there’s no going back to guesswork.
Safety Precautions When Using Punching Tools
When you’re diving into a project that requires the use of punching tools, safety should be a top priority. I’ve seen my share of injuries that could’ve been avoided with just a few extra precautions. Let me share some golden nuggets of advice to help keep you on the right side of safety when you’re working with these sharp instruments.
First off, never underestimate the importance of hand protection. You might think you’re precise enough, but even the steadiest hand can slip. I’ve found that wearing a good pair of leather gloves not only gives better grip but also acts as a protective barrier between the tool and your skin. Trust me your fingers will thank you later.
Also, pay attention to your workspace. Punching on an unstable surface? That’s just asking for trouble. Always make sure you’re working on a flat, non-slip surface. If your table shifts, your tool can too, and next thing you know, you’re nursing a nasty cut.
Here are some extra tips that might not come to mind right away but are just as crucial:
- Ensure proper ventilation if you’re working with any materials that produce fine dust or debris.
- Keep your tools sharp. A dull tool requires more force, and more force means less control.
- Store tools safely. I’ve learned the hard way that leaving sharp tools out in the open is a recipe for disaster. Keep them in a protective sheath or toolbox when not in use.
As a matter of fact, take your time. Rushing a project is a quick way to get hurt. Give yourself space and time to work methodically. There’s nothing worse than finishing a project with a bandaged hand because you cut corners literally.
How to Achieve Clean, Professional Holes
Achieving crisp, professional-looking holes when working with leather can be an art in itself. Trust me, you don’t want jagged edges or misshapen holes ruining your masterpiece. From my own projects, I’ve learned a few key tricks that ensure your leather looks flawless every time.
First and foremost, start by marking your hole positions. Precision is crucial, so I recommend using a fine chalk or a tailor’s pencil to make tiny, clear marks on the leather. Avoid freehanding trust me, you’ll regret it later.
When you’re ready to punch, make sure the leather is on a stable, hard surface. A wooden block or thick cutting mat works great. Anything softer will cause uneven pressure, which leads to imperfect holes.
Here’s a quick rundown of my top tips for those neat, clean holes:
- Proper alignment: Ensure the tool is exactly perpendicular to the leather. A slight tilt can distort the hole.
- Firm pressure: Apply even, consistent force. Don’t try to rush by hammering too hard or too soft just steady and solid.
- Sharp tools: I can’t emphasize this enough keep your punch sharp! Dull tools leave rough edges, and it’ll show in the final product.
- Rotary motion: If you’re finding it difficult to punch all the way through, a slight twist of the wrist as you press can give you that extra bit of leverage.
Also, inspect each hole after punching. If necessary, use a small file or sandpaper to smooth any rough edges. That attention to detail will make your finished project look much more polished.
Need Help? Hereโs More
What is a leather hole punch called?
A leather punching device is commonly referred to as a leather punch or hole punch. This tool is specifically designed to create precise holes in leather for a variety of purposes, such as attaching hardware like rivets, snaps, or eyelets. There are different types of leather punches, including rotary punches, which have multiple hole sizes, and single punch tools, often used for more detailed or intricate projects.
What tool do you use to punch leather?
To punch leather, you typically use a leather punch, which can be either a rotary punch or a hole punch. Rotary punches have multiple rotating heads for various hole sizes and are ideal for punching round holes. Another common tool is the drive punch, where you strike the punch with a mallet to make a clean hole. For specialized work, tools like chisels or pricking irons may be used to create stitching holes.
What helps you punch holes on leather?
Several factors help in punching holes on leather efficiently, including the right tool, such as a leather punch, and a sturdy surface like a cutting mat. Additionally, using a mallet or hammer with a drive punch tool ensures proper force to penetrate thicker leather. Marking the spots before punching with a ruler or template can help ensure accuracy, and conditioning the leather can make the process smoother, especially when working with dense or stiff materials.
What do you call the leatherworking tool used for punching or marking stitching holes?
The leatherworking tool used for punching or marking stitching holes is typically called a pricking iron or chisel. A pricking iron helps mark evenly spaced holes for stitching, while a stitching chisel actually punches through the leather. Both tools are essential for preparing leather for hand-stitching by ensuring the holes are placed correctly and consistently, resulting in clean, uniform stitches.
How to punch a hole in thick leather?
Punching a hole in thick leather requires a heavy-duty leather punch or a drive punch. To do this, place the leather on a sturdy surface such as a cutting board. Mark the hole’s location and position the punch on the leather. Use a mallet to strike the punch with controlled force, ensuring a clean cut through the material. You may need to apply more force for thicker leather, or use a rotary punch with a reinforced mechanism designed for thicker materials.
What is a leatherworking tool called?
A leatherworking tool can refer to a wide range of instruments, depending on the task, but the general term for these tools is ‘leather tools’ or ‘leathercraft tools.’ These include punches, awls, chisels, knives, burnishers, and pricking irons. Each tool has a specific purpose, such as cutting, shaping, stitching, or embellishing the leather, and is designed to handle the unique properties of the material.
How do you punch leather without a punch?
If you don’t have a dedicated leather punch, you can still create holes using alternative tools like a sharp awl, nail, or even a heated needle for small holes. Place the leather on a firm surface, mark the hole, and carefully push the awl or other tool through the material. While not as clean as using a punch, these methods can work for less formal projects. For larger holes, a drill with a small bit can also be used, though caution is required to avoid tearing the leather.
What is the best surface to punch holes in leather?
The best surface to punch holes in leather is a cutting mat or a piece of scrap leather. These surfaces are soft enough to protect your punch’s sharpness while providing resistance for clean cuts. Alternatively, a block of dense plastic or rubber can also work well. Avoid hard surfaces like concrete or metal, as they can damage the punch and prevent the tool from cutting cleanly through the leather.
How do you use a leather punch kit?
To use a leather punch kit, start by selecting the appropriate punch size based on the hole you need. Mark the spot on the leather where the hole should be placed. Position the punch tool on the leather and ensure it’s aligned. If using a rotary punch, simply squeeze the handle to punch through. If using a drive punch, place the punch on the mark and strike it with a mallet. A leather punch kit often includes various punch sizes and a hammer or mallet.
What is the name of the tool that punches holes?
The tool that punches holes is typically called a hole punch or leather punch. In leatherworking, it can be a rotary punch or a drive punch, depending on the type of hole and the project. Rotary punches have adjustable heads for different hole sizes, while drive punches are singular, requiring a mallet or hammer to create the hole by force.
What is a leather piercing tool?
A leather piercing tool is commonly referred to as an awl or a stitching awl. This tool is used to pierce or create small holes in leather for stitching or marking. Awls are pointed and sharp, allowing for precision work, especially in hand stitching where you need to guide the needle through pre-made holes. Some piercing tools also come with interchangeable heads for various types of holes.
What is a leather sharpener called?
A leather sharpener is often called a strop or sharpening stone, specifically used to maintain the edge of leathercraft knives and other cutting tools. A strop, typically made of leather, is used to refine the blade’s sharpness after it has been honed on a sharpening stone. Keeping tools sharp is essential in leatherworking to ensure clean cuts and reduce the risk of damaging the leather.
This is such a solid guide on maintaining tools! I used to be so lazy about sharpening and cleaning my punching tool, and I could never figure out why my results were so inconsistent. Once I started paying attention to keeping it sharp and oiling the joints, it was like night and day. I especially relate to your point about storage after neglecting to wrap my tools for a while, I started noticing a bit of rust, so now I make sure to store them properly with some silica gel packets. Trust me, people following these tips will save you a lot of frustration and extend the life of your tools big time. Future-you will definitely be grateful for the extra care!
I love how you broke down the process of using a hole punch! It’s such an underrated tool that can make or break a project. I remember my first attempt at using one I was so excited, but it quickly turned into a mess because I rushed it. Now, I always take your advice to heart: marking where I want the hole is a must! The precision tip is especially crucial for those of us who are perfectionists at heart. I’ve also learned that applying steady pressure really helps; too much enthusiasm can lead to those frustrating wonky holes! And punching into a soft surface? Such a small detail but a lifesaver! I had no idea how much that would improve my results until I tried it. Thanks for sharing these fantastic tips definitely going to keep them in mind for my next project!
This section really hit home for me! When I started leather crafting, I made the rookie mistake of using my kitchen table as a workspace, and let me tell you, that didn’t end well! I’ve learned that investing in a good cutting mat is essential, just like you mentioned. It not only protects my surfaces but also helps me keep my tools in better shape. And those high-quality chisels you mentioned? Game-changers! They save so much time and effort during crafting sessions. I can relate to your journey of trial and error; I’ve had my fair share of mishaps, especially with marking tools. Finding the right marking pen truly enhances the accuracy of my designs, making the process so much smoother. Now, I can’t imagine working without my trusty mallet either it’s like my crafting sidekick! Keep sharing these insights; they’re super helpful for us fellow crafters!
I absolutely love this analogy of choosing tools as selecting a dance partner! It resonates so well with my own experiences in crafting. In the beginning, I found myself overwhelmed by all the options, too. I remember when I first tried my hand at sewing; I gravitated toward a fancy, expensive sewing machine thinking it would automatically make me a better crafter. Spoiler alert: it didn’t! After some trial and error, I realized that finding a tool that suits my style and project needs made all the difference. Now, I prioritize comfort and functionality over flashiness. I can’t stress enough how much easier my projects have become since I switched to tools that actually feel right in my hands. The recommendation part is golden too nothing beats a solid tip from someone who’s been there! Happy crafting, everyone!
The steel versus brass debate is a classic, and I love how you’ve presented both sides! I lean toward steel for its durability, especially when I’m tackling larger projects. However, I can’t resist the elegance of brass tools, especially for more delicate tasks. They add such a beautiful touch to any workspace! I once made a bracelet using brass tools, and the results were stunning. Plus, the corrosion resistance is a big plus for outdoor projects. Ultimately, it’s about knowing what works best for each project, and your insights really help clarify that. Thanks for the thoughtful comparison!
Your take on hole size is spot on! I can’t tell you how many times I’ve wrestled with materials due to improper hole sizing. That giraffe analogy is hilarious and so accurate! Finding that Goldilocks zone has truly transformed my projects. I remember the joy of nailing the perfect size for a leather bag I made, and it felt like magic. Playing around with sizes definitely adds a fun twist to the crafting process, so thanks for the reminder to keep experimenting!
I love how you’ve highlighted the essential features to look for in crafting tools! Adjustability has saved me so much time and hassle, especially when working on projects that require different hole sizes. Ergonomics is another game changer; I remember my hands cramping up during long sessions until I found a comfortable tool. It really does make a difference! And I couldn’t agree more about material quality. Investing in durable tools has paid off in the long run, allowing me to focus on the creative process instead of worrying about whether my tools will hold up. Thanks for sharing such practical tips!
I love your breakdown of different hole-making tools! The revolving punch is truly a favorite of mine as well; it’s like having a toolbox in your hand. Switching sizes on the fly makes it incredibly versatile for any project! I agree that the single-hole punch is a classic; I often use it for adding those little details that make a big difference. Your mention of the chisel punch is spot on! The clean lines it produces are so satisfying and really do help achieve that professional finish. Exploring these tools has definitely added a new layer to my leather projects. It’s fun to see how each tool can influence the final look. Happy crafting!
Your insights on mastering leather crafting tools are spot on! I especially appreciate your tip about using a cutting mat or scrap wood as a sturdy surface such a simple yet crucial step. I made the mistake of punching on a soft surface once, and let me tell you, the results were far from pretty! Marking the design beforehand has become my go-to practice now; it saves me from those “oops” moments. And yes, testing on a scrap piece is so vital! I often find myself getting carried away in excitement, but that practice really makes a difference. Your advice about applying even pressure is something I’ll definitely keep in mind to avoid those jagged edges. Thanks for sharing these valuable tips; they will undoubtedly help many of us level up our leather crafting skills. Here’s to crafting with confidence!
I completely resonate with your enthusiasm for the leather punching tool! It really does feel like a magic wand, doesn’t it? I remember when I first tried it; the thrill of punching those precise holes transformed my projects from basic to beautiful. The way you described feeling like an artist chiseling marble truly captures the essence of crafting. Plus, the variety of punch sizes is a game changer! I love how versatile it is, from making intricate patterns on wallets to sturdy belts. It’s amazing how such a simple tool can elevate our creativity. Here’s to many more satisfying punches!